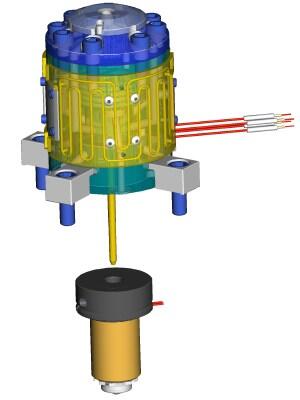
At K 2013 (stand F12, hall 2) Thermoplay introduces the new FN series nozzle family that will replace the current F series. The main reason for this innovation is to reduce the maintenance time to replace the heater and the thermocouple, which can now be performed without having to remove the nozzle tip. The FN nozzles are available in the diameters 16, 24, 32 and 46 mm with the same standard lengths of the F series.
Besides the versions with diameter 16, 24 and 32 mm are provided with a special bimetallic insert in titanium and tempered steel inside the tip group, thus allowing a wider area of contact with the mould. This characteristic reduces the risk of wear in the gate area and possible plastic leakage, also decreases the thermal exchange between nozzle and mould resulting in reduced power consumption. The gate geometry of the FN series are unchanged in comparison to the F therefore can be replaced with the new nozzles without any additional machining in the mould.
Always belonging to the FN series, the screw in nozzles can be mounted to the manifold with different inclinations for guaranteeing the perpendicularity with the moulded surface thus following the geometry of the moulded part. In particular the new version with 60-mm diameter is provided with an internal channel of 25 mm to facilitate optimal flow of plastic material. Furthermore, for this version, a special manifold has been realized with a channel of 30 mm diameter. The valve pin has a diameter up to 10 mm to get a wider injection point.
The lengths of these nozzles can be personalised as required, up to a maximum of 696 mm with multiple heaters. The screw-in nozzle is available with or without valve gate. The shut off group is compact (minimum height: 83.5 mm) to simplify the mould machining. In addition the pin can be adjusted without removing the group from the mould.
Finally, the new type of single valve gate has been developed to achieve optimal balanced system. In fact, it has four flow channels, which divide the melt flow in homogeneous and uniform way. Thanks to a special innovation it is possible to replace the nozzle body with alternative variants both in diameters and lengths, keeping the original head and the shut off group, then saving in costs. The tip group is provided with a new pin guide that allows an optimal centring of the pin in proximity of the gate to reduce the wear of the cavity.
The pin drive bushing inside the shut off group is provided with a wide seal to reduce the material stagnation inside the single nozzle. As consequence, it is no longer necessary to eliminate the gases produced by the polymer during the moulding process.