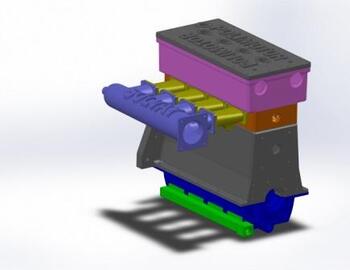
It will be called Polimotor 2 and it will be produced entirely of plastic materials by Solvay Specialty Polymers. The all-plastic automotive engine will be tested in a race car next year, demonstrating the company’s unique and industry-leading advanced specialty polymer technologies in light-weighting through metal replacement.
The collaborative project will ultimately set the stage for innovative breakthroughs in future commercial automobiles. Automotive engines typically are made entirely of metal and are the single heaviest part in a car. Polimotor 2 aims to develop an engine weighing about 63-67 kg, or about 41 kg less than today’s standard production engine.
“The Polimotor project is yet another pioneering opportunity for Solvay Specialty Polymers to bring its innovations to the forefront and to expand its lightweighting offerings. Through this partnership we will further challenge our boundaries, showing all the more that our high-performance polymers are solutions in reducing weight and lowering fuel consumption, and that they are a key contributor in diminishing carbon dioxide emissions”, said Augusto Di Donfrancesco, president of Solvay’s Specialty Polymers Global Business Unit.
In Polimotor 2, Solvay will replace up to ten metal engine components - including the water pump, oil pump, water inlet/outlet, throttle body, fuel rail, cam sprockets and others - with parts made from seven of its high-performing thermoplastic materials. Polymers targeted for use include Torlon polyamide-imide (PAI), Amodel polyphthalamide (PPA), KetaSpire polyetheretherketone (PEEK), AvaSpire polyaryletherketone (PAEK), Radel polyphenylsulfone (PPSU), Ryton polyphenylene sulfide (PPS) and Tecnoflon VPL fluoroelastomers.
The Polimotor 2 four-cylinder, double-overhead CAM engine will ultimately be installed in a Norma M-20 concept car in 2016 for competitive racing at Lime Rock Park, Conn. Solvay contributed a major role toward the success of the first Polimotor engine, conceived by US engineer Matti Holtzberg in the early 1980s.