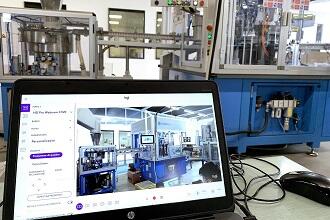
In this recovery phase after the emergency caused by the Covid-19 virus, before everything returns as before, it’s necessary to find out new solutions to meet the new needs caused by the pandemic.
For this reason Gefit successfully finalized its first online FAT: by using cameras and permanent connection, customers have been able to actively participate in the FAT of an index assembly machine, remaining constantly in audio visual contact with Gefit engineers, working at their plant.
Customers just had to download an app on their devices and then follow all operations on the machine in real time, being also able to interact directly and ask our technicians for specific interventions.
This way it has been possible to monitor the performances and communicate with GEFIT team in real time, with a complete remote interaction and without any impact on the previously agreed time schedules for the machine delivery.
A successful experience that will be also extended for the testing of moulds, until the situation gets finally back to normal.
Furthermore, thanks to the use of special smart glasses equipped with wearable headset, a new frontier will be torn down: Gefit will be able to provide customers from all over the world with an innovative remote assistance service, complete with audio and video, that makes the operators on site completely free to move and put the received indications into practice.