Inverter per ogni esigenza della trasformazione
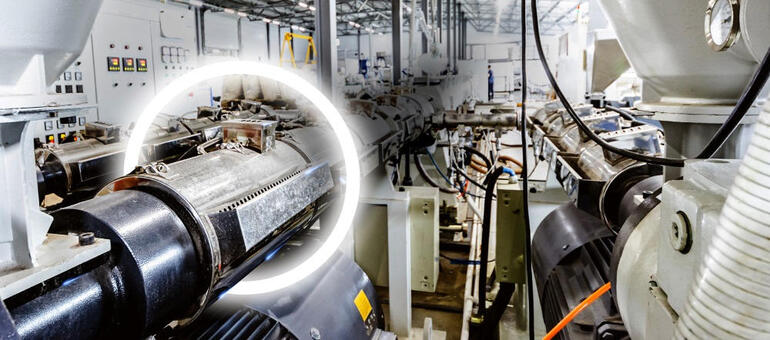
Attiva nella produzione di inverter intelligenti per il controllo dei motori elettrici, Danfoss si presenta a Plast 2023 con una vasta gamma di soluzioni per le macchine per la lavorazione di materie plastiche e gomma, a cominciare inverter della famiglia Vacon NXP in esecuzione Liquid Cooled. Si tratta di un sistema molto robusto che, grazie al raffreddamento a liquido, consente di ottenere fino al 25% di risparmio rispetto ad analoghe soluzioni raffreddate ad aria. La modularità ne consente l’impiego in un vasto numero di combinazioni, da un singolo inverter fino a sistemi composti da più moduli connessi via DC bus, con potenze da 75 kW a 5,3 MW in bassa tensione (400 V e 690 V). Anche silenziosi, questi inverter rappresentano la soluzione ideale per i costruttori di macchine, che possono trarre beneficio anche dagli ingombri particolarmente contenuti, un fattore che ne agevola l’installazione diretta in campo.
Ai modelli raffreddati a liquido se ne affiancano altri raffreddati ad aria, che dispongono delle medesime caratteristiche di robustezza, compattezza e affidabilità, ma che consentono di gestire potenze fino a un massimo di 2 MW. Selezionando le configurazioni più idonee è possibile ottenere prestazioni ottimali unitamente a notevoli risparmi energetici, efficientando il processo non solo in termini di velocità e precisione, ma anche in ottica di consumi elettrici.
Un’altra delle caratteristiche che rende la famiglia degli inverter Vacon NXP ideali per le applicazioni dove le potenze in gioco sono ragguardevoli e gli spunti di corrente molto elevati, come di norma accade nei processi di lavorazione di plastica e gomma, è il basso livello di armoniche. Con un valore di distorsione totale armonica THDi inferiore a 5%, i Vacon NXP offrono un’eccellente soluzione che consente di rispondere al meglio anche ai più stringenti requisiti di qualità della rete elettrica. Tutto ciò senza la necessità di sovradimensionare i trasformatori o i cavi di alimentazione in ingresso e mantenendo inalterata la disponibilità di funzioni come la frenatura rigenerativa (mediante DC bus) e l’innalzamento della tensione per la piena erogazione della massima potenza.
Laddove la continuità di esercizio è invece un’esigenza assoluta - si pensi alla necessità di non interrompere mai un processo continuo come, per esempio, la mescolazione della gomma - gli inverter Danfoss possono essere efficacemente utilizzati per implementare architetture di comando motore con ridondanza a caldo. Per ciascun motore è infatti possibile installare, dimensionandoli opportunamente, fino a quattro inverter standard in parallelo. Una speciale funzione di condivisione del carico fa sì che, nel caso in cui un drive registrasse una condizione di errore, siano gli altri a subentrare a caldo, garantendo la continuità di esercizio e allertando nel contempo l’utilizzatore.
L’offerta Danfoss include anche VLT FlexMotion, un sistema di motion control integrato che, in base alle specifiche necessità, consente di implementare soluzioni servo centralizzate e decentralizzate, garantendo modularità e massima flessibilità di integrazione. VLT FlexMotion è un sistema di servo-azionamento universale progettato per soddisfare le tipiche esigenze dei costruttori di macchine, che necessitano di flessibilità e libertà per integrare motori, controllori e dispositivi multivendor nei loro sistemi di produzione. VLT FlexMotion supporta tutti i più diffusi protocolli basati su Ethernet Industriale - tra cui EtherCAT, PowerLink e Profinet, anche in versione IRT - nonché la programmazione in standard IEC 61131-3. Il supporto delle librerie motion conformi a PLCopen rende il sistema ancora più flessibile e facile da integrare nei diversi ambienti di progettazione, con la tecnologia motore che può quindi essere liberamente scelta dal costruttore senza alcuna costrizione.
Nel settore della plastica e della gomma VLT FlexMotion si è dimostrata una soluzione vincente in molte applicazioni. Un caso emblematico è quello della produzione di manufatti cavi ottenuti per soffiaggio (taniche, contenitori, serbatoi ecc.), dove il costruttore è riuscito a implementare un sistema di motion control integrato ad alte prestazioni in grado di gestire in maniera sincrona tutti gli assi macchina: dall’ingresso del polimero in macchina fino all’espulsione del prodotto finito. Tutto con un unico sistema.