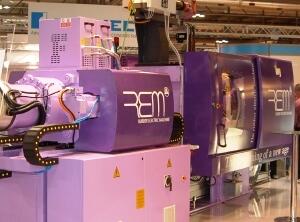
According to IMG, a manufacturer based in Capriano del Colle, near Brescia (Italy), who has been offering them for the injection moulding of elastomers, the electric presses of the REM range (an acronym which stands for Rubber Electric Machine) guarantee 30% more energy savings. As a result, these machines satisfy a major need in this field, where, with longer cycles, the power consumption reduction during the dead processing times is reflected in significant savings.
The REM presses feature a double toggle-joint five-point clamping unit and a floating platen sliding on ballscrew guides without bushings. This solution prevents flashes or foreign particles from accumulating on the tiebars. The injection unit with reciprocating screw also slides on ballscrew guides and is driven by an in-line servomotor delivering all the torque needed for processing elastomers. In addition it can generate a specific pressure of 2400 bar. The motors without transmission parts are considered the ideal solution for ensuring maximum clamping force, and more generally, excellent cycle repeatability.