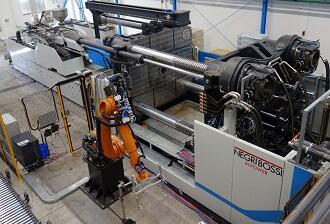
When he referred to Negri Bossi a couple of years ago, Michael Bechtel, the founder of MB Spritzgusstechnik in Marktoberdorf (Germany), had a Vision: “Recycled Plastic as raw material to be re-used for a longer lifetime”. Today, he has one of the most advanced plastic injection technology installed in his factory to get recycled plastic converted into industrial pallets: a Negri Bossi Bi-Power VH2700-56000, a two-platen giant with 27,000 KN clamping force and injection capacity of 28 kg of HDPE, equipped with servo electric screw rotation, special screw profile projected for complex recycle materials.
The machine is supported by complete Sytrama automation with 6-axis robot and the local partner Zimmermann-KT supplied a sophisticated extensive peripheries technology. MB Spritzgusstechnik, a 13-year-old injection moulding reality, has 160 employees and 30 machines installed where the newest Bi-Power plays as a strategic move toward a sustainable growth and technologic advancement.
Negri Bossi supplied the heart of the system: a Bi-Power 2700 ton with a complete automation, which were perfectly installed and commissioned by Negri Bossi technicians team in a record time, thanks to the professional client’s technical team. A complete training was then carried out to make sure the maximum skill level of the operators. The system was monitored by Amico tele-service system to guarantee the highest efficiency.
The injection unit of Negri Bossi Bi Power is designed so that a uniform melting and homogenizing of the recycled material is possible. It was for this purpose equipped with a special barrier screw and feeder aids for recycling material. Alternatively, plastic granules with a long glass fibre or mineral reinforcement can be processed by using a 3-zone screw. The necessary screw exchange for material exchange is easy to implement on the swivelling injection unit, and thanks to the servo electric screw rotation, screw lifetime is at the maximum despite the complex material resistance.
Control of
BI Power VH2700-56000 is user-friendly thanks to an intelligent,
self-explanatory menu. Employees do not need expensive extra training and long learning
phases, especially with the support of Amico system, the Negri Bossi
tele-service assistance, which allows a fast reaction and immediate
problem-solving.
On the other hand, Michael Bechtel can reduce the spare parts warehouse because of the individual components of all leading European manufacturers used in the machine, entering the "availability guarantee" for the next 15 to 20 years and are easy to get on the market. "There is nothing exotic in it, neither a cheap valve from the Far East, nor an electric part, which must then be ordered that takes long to be delivered", Bechtel recognizes the quality. In the long-term the warehouse can significantly be reduced through the use of the same components of the manufacturer in all its 70-7000 ton series. The use of the same electrical components, hydraulic and pneumatic valves and controls secure machine availability. “With this partner I can create a same-parts-strategy”. When the bigger machine goes down, then, the part can come from a smaller machine, due to the component equality, as a plug-in card can be removed and installed in the big machine, so that immediately comes to running. This minimizes my inventory that I need to stockpile and ensures the constant availability of my equipment”.