Pressa dell'anniversario per i 100 anni di Arburg
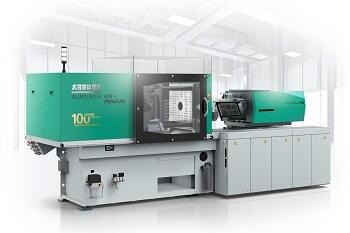
Per i festeggiamenti per i suoi cento anni di storia, che hanno preso il via il 16 febbraio con un evento di gala presso la sede di Lossburg (Germania) e si protrarranno fino ai Technology Days, in programma sempre a Lossburg dall’8 all’11 marzo e che per l’occasione quest’anno prenderanno il nome di Anniversary Days, il costruttore di macchine a iniezione e sistemi per la stampa additiva Arburg lancia la pressa ibrida dell’“anniversario” Allrounder 470 H in versione Comfort, Premium e Ultimate, di cui sottolinea eccellente risparmio di energia e risorse, efficienza, facilità di utilizzo e affidabilità.
Secondo Gerhard Böhm, direttore vendite e assistenza di Artburg, "gli azionamenti elettrici stanno diventando sempre più importanti, non da ultimo in termini di efficienza energetica. Nella nuova Allrounder 470 H, abbiamo creato proprio la macchina ibrida di cui gli utenti hanno bisogno oggi e in futuro; una macchina che non era ancora disponibile sul mercato in questa forma". Per il costruttore, la pressa dell'anniversario risulta particolarmente interessante per i trasformatori alla ricerca di un'alternativa a risparmio energetico rispetto alle presse idrauliche: l'unità d'iniezione idraulica riduce i costi di acquisto ed è estremamente robusta e gli azionamenti elettrici del gruppo di chiusura riducono il fabbisogno energetico, a vantaggio di costi operativi e impronta di carbonio.
"La nuova generazione di macchine incorpora molte innovazioni tecniche che sono disponibili solo da Arburg. Durante la progettazione della nuova Allrounder 470 H, abbiamo notevolmente migliorato la nostra tecnologia per ottimizzare l'impronta energetica e ridurre i tempi di ciclo", ha aggiunto Guido Frohnhaus, direttore dello sviluppo tecnologico e ingegneristico. Rispetto alle presse idrauliche, la nuova Allrounder 470 H si contraddistingue per un bilancio energetico migliore fino al 50% e una riduzione annua di 12.000 kg di emissioni di CO2. Tra le novità introdotte troviamo il nuovo concetto di gestione dell'olio, in attesa di brevetto, la suddivisione della portata per i movimenti simultanei degli assi secondari idraulici e l'uso esteso del sistema servo-idraulico Arburg. Anche i tempi di funzionamento a vuoto sono stati ridotti di un terzo.
Il nuovo concetto di gestione dell'olio si basa su un serbatoio migliorato, un alloggiamento del filtro dell'olio abilitato alla pressione differenziale e sulla manutenzione predittiva per la sostituzione del filtro e l'ispezione della pompa dell'olio, garantendo un funzionino a basso fabbisogno energetico e di risorse. Il nuovo concetto di gestione dell'olio, inoltre, riduce il consumo di energia e di acqua di raffreddamento e aumenta la durata dei singoli componenti. L'olio idraulico caldo e contaminato viene separato da quello freddo e pulito nel contenitore dell'olio. Insieme al volume di ritorno costantemente filtrato e raffreddato e alla guida mirata del flusso, la qualità dell'olio viene migliorata con un consumo di olio inferiore circa del 35%. Il calore residuo della macchina può essere utilizzato per preriscaldare l'olio e non rifluisce nel circuito dell'acqua di raffreddamento come calore residuo. La suddivisione della portata della pompa idraulica consente di azionare, contemporaneamente a quello principale, un ulteriore asse secondario, con effetti positivi sulla produzione e sull'efficienza energetica, in particolare con le macchine ibride Allrounder H, riducendo tempi di ciclo e consumi energetici.
Il sistema servo-idraulico Arburg (ASH), già collaudato nelle Allrounder idrauliche ed elettriche, è stato integrato nelle macchine Allrounder 470 H Comfort e Premium. Il sistema consente un funzionamento particolarmente efficiente dal punto di vista energetico e a basse emissioni, poiché il servomotore a velocità controllata e raffreddato ad acqua adatta continuamente il sistema di azionamento al fabbisogno di potenza effettivo. Ciò significa, per esempio, che quando la macchina è ferma anche l'azionamento della pompa è fermo, consentendo di risparmiare fino al 50% dell'energia, soprattutto nei processi con lunghi tempi di raffreddamento. Allo stesso tempo anche i requisiti di raffreddamento e il livello di rumorosità della macchina sono notevolmente ridotti.