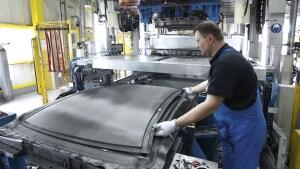
At JEC Composites 2014, to be held in Paris from March 11 to 13, Cannon will present its most recent developments in the fields of processing technologies for glass and carbon reinforced composites and for thermoforming.
For the epoxy-based fast RTM moulding of automotive, sport and leisure components, the company will propose the Estrim technology. Besides dedicated preformers, polymerisation clamps and moulds, the E-System high-pressure metering and mixing equipment guarantees very fast demoulding times and perfect distribution of the resin across the entire mould surface. In addition to a standard high-pressure injection system in closed mould - now available for three different methods of injection - two methods for the distribution in open mould of the epoxy resin over the carbon fibre inserts have been developed: Estrim LLD for the application of a liquid layer; Estrim SLD for a spray application. These methods reduce the specific pressure in the polymerization press and the investment in clamping equipment. Still for the automotive industry, the innovative compression moulding line for LWRT (Light Weight Reinforced Thermoplastics) will be proposed for the production of thin and light large parts such as engine shields.
The low pressure DX machines will be presented for the infusion of epoxy resins into blades for off-shore and conventional wind turbines. The range now includes a three-component model that allows for the flexible use of two different hardeners in order to obtain different reaction profiles in accordance with the size of the moulded part. A degassing unit for resin and a glue dispenser for the application of two-component adhesive will complete the series of solutions for this sector.
Also the new InterWet mixing head for the coinjection of polyurethane and glass fibre will be destined to the transport and wind-power industry for the production of lightweight and wide structural elements, able to replace - with much faster production cycles - similar manufacturing methods based on low-pressure RTM injection. A new design of the mixing chamber significantly improves its efficiency in terms of glass fibre wetting and in-mould distribution. A completely redesigned chopping unit allows for higher glass fibre output and longer runs between the replacement of the chopper's blades.
Finally, the first industrial results of the CRESIM (Carbon Recycling by Epoxy Special Impregniation) project will be introduced. It is aimed at the development of a technology for processing composites obtained with recycled carbon fibres.