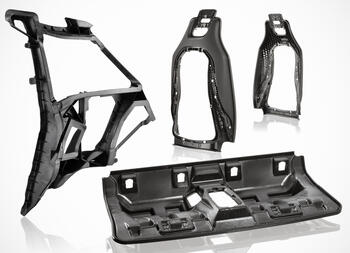
For several innovative components in the BMW i3, the electric vehicle from BMW, Basf supplies versatile plastics and supported part development with extensive construction know-how. These include the backrests of the front seats, key reinforcement parts in the carbon fiber body, and the rear seat shell.
The seat backrest in the driver’s and passenger seats is the first injection molded and uncoated structural component made from polyamide to have a visible surface and to be used in the vehicle interior. This lightweight hybrid component, weighing only 2 kg, embodies all the know-how of the Global Seat Competence Team. The backrest, which integrates multiple functions, is made from a highly UV-stable polyamide 6 compound especially for such applications (Ultramid B3ZG8 UV). As well as providing sufficient rigidity, this material also ensures adequate elongation and toughness to meet the mechanical requirements of BMW, and this within a temperature range of -30° C to +80° C.
The seat backrest owes its final, complex and above all very slim shape to the early use of Basf’s universal simulation tool Ultrasim. Thanks to the precise numerical simulation of the materials used for the backrest, release lever and belt guide, the calculated behavior in the crash simulation matched the subsequent tests very accurately.
The i3’s carbon body contains PBT structural parts between the inner and outer shell. The largest component and the first of its kind is a so-called integral component located in the rear side area between the carbon fiber body shells. Apart from its load-bearing function in the event of a crash, it also serves to keep the two body shells apart and forms the rear opening for the side window.
The PBT Ultradur B4040 G6 is ideal for this since it is dimensionally stable irrespective of surrounding climate conditions and offers the necessary buckling resistance. The simulation has made a major contribution here to low-warpage production and the glass fiber orientation suitable for the occurring loads. The injection-molded component comprises several smaller components planned in the past thus reducing complexity and costs. More than two dozen smaller Ultradur components with a combined weight of around nine kilograms are integrated in other areas of the vehicle’s body where they provide reinforcement and achieve the desired acoustics.
The self-supporting rear seat shell is made from Elastolit polyurethane system. The component integrates a variety of functions such as the cupholder attachment and storage tray, saving on both assembly work and weight. A key feature is its wide process window together with its high fatigue strength and damage tolerance. Because of the material’s special properties the crash-relevant part meets the stringent safety requirements by BMW despite its wall thickness of just 1.4 millimeters.
The PU structural foam Elastolit D is used as a reinforcing material in the whole roof frame, including the A-pillar. The highly pressure-resistant foam is manufactured to a carbon sandwich composite, thus supporting the structural rigidity of the vehicle.
The i3 incorporates many other parts which have already been established in a number of vehicles:
- the fuse box made of Ultramid B3ZG3, which meets the stringent demands on rigidity and tensile strength, as well as a high-voltage connector made of Ultramid A3EG6; apart from that also cable sheathings and cable glands made of the polyurethanes Elastollan and Elastoflex
- in the vehicle interior, the PU semi-rigid foam Elastoflex E is utilized for back foaming the instrument panel, while the C-pillar cover is made of Ultramid B3ZG3
two different Elastoflex E polyurethane foams are employed in the roof construction for improved interior acoustics: in the roof liner, forming the core material of a sandwich composite which has excellent thermoformability and high rigidity; an extremely low-density, open-cell Elastoflex E foam is used as the basis for acoustically effective parts
- in the module production of the optional sliding roof, the UV and weather-resistant glass encapsulation system Elastolit R 8919 is applied. The frame of the sliding roof is made of Ultradur B 4040 G6, a low-warpage PBT/PET-blend
- lightweight spring aids made of Cellasto, the micro-cellular special elastomer.
Finally, coatings division supplies basecoats in four colors which meet the requirements of the coating of add-on components and of the painting processes involved.