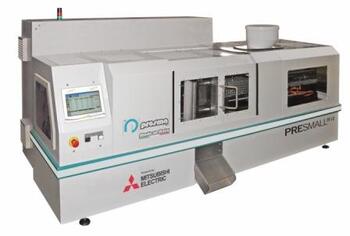
At Plast 2015, Presma’s booth (stand B 21, hall 22) is dedicated to two different machine ranges, foamed thermoplastic and the thermosetting rubber injection process. The first is a special rotary machine range: Roto T2/48 Elettra, full electric, specifically for the production of corks made in foamed thermoplastic resins. This model is equipped with 48 double cavity mouldholders and two injection groups which allow the moulding of 4 different cork types, that can be manufactured in two different materials/colours. The “transfer” injection groups are driven by electric motor controlled by an inverter for the plasticizing screw, and by a brushless motor for the punch. The full electric operation gives the average consumption of 6,5 kW/h, while producing 3000 corks/h, keeping consistent quality, superior to the corks moulded with the previous hybrid models. The Roto Logic control, developed by Presma, enables you to set 2 different dosages on each injection group for 1 or more single cavity moulds to sample corks that are different in shape and weight, within the same production cycle.
Using the touch screen interface unit, it is possible to manage all moulding parameters through different sensors that check the machines automatic functions, its alarms and its cycle reset, in case of jamming. The machine is offered with remote assistance and is adapted for the possibility of adding Insert loaders for automatically loading the mould (i.e. wooden or plastic heads for T-corks).
The second machine Presmall R12 represents a novelty in the rubber moulding field. It is an evolution of the fully electric Mini model, specific for rubber and silicone moulding; during Plast it will be possible to see the machine running, equipped with a 2-cavity mould and a specific extruder for solid silicone.
Its main feature, which diversifies this machine from its “little sisters”, with and without tie-bars for thermoplastics, is the 120 KN clamping unit with 4 tie-bars; the Mitsubishi control board has been kept, as it can drive up to 16 axis, 3 of them as standard equipment for the injection process. Thanks to the use of a high speed optical fibre net and a high resolution encoder, the control unit checks and promptly adjusts the position of any actuator by 0,44 milliseconds, thus granting the precise positioning with an accuracy within tenths of a micron. The absolute encoders are equipped with a back-up battery, allowing them to skip the zero-set usually necessary for the start of electrical machines.