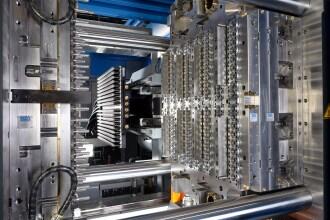
Iran’s largest producers of PET preforms is banking on Sipa in its latest round of expansion. Khosh Form, which has operations in the cities of Mashhad (Khosh Form Toos) and Qazvin (Khosh Form Caspian), has, other than 10 different Husky machines, 7 XForm 500 preform injection molding system at both locations, all of them running with 96-cavity molds. The XFORM 500 systems produce preforms for carbonated soft drink, 38-mm neck dairy products and for mineral water bottles. The XForm 500 has the capability to run legacy tooling as well.
Khosh Form has been on a steep growth path since it started making PET preforms in 2003. Both of its sites have benefitted from surging demand for drinks bottled in PET, both at home and in neighbouring countries. It has connections to numerous major international brand owners.
The company makes preforms weighing as little as 10.4 g and as much as 54.75 g, for bottles ranging in size from 300 to 2500 ml. It has an extensive park of molds, so investing in the XForm 500, with its ability to accept large molds from all the top suppliers, makes a lot of sense.
“The full compatibility of the Sipa XForm with our existing equipment is a great advantage for us”, says Hajrezapour, owner of Khosh Form. “This has given us extra versatility in our production. And the XForm 500 system produces high quality preforms with high consistency. The machines have already proved to be very reliable, and we have quickly grown accustomed to the new platform”.
“With its latest technology, Sipa has made a big leap forward. We appreciate this, because at Khosh Form we look only for the best in class. Our customers own the most important international brands in the beverage business, and they audit our production regularly - so we cannot compromise on the quality of our equipment”.
Khosh Form
has only recently come to Sipa. After it heard good things about the company
from existing Sipa customers in the region, top executives had a close look at
an XForm installation. They carried out a technical survey and set the system
against its competitors. In a complete comparison, taking into consideration
such critical factors as cycle times, running cost and initial investment, the
XForm came out on top.
Sipa has the extra advantage of being able to provide local service from technicians close by - another important selection criterion for Khosh Form.
Khosh Form appreciates the XForm 500 injection molding system as a solid tool with a robust design and construction, says Sipa’s Stefano Baldassar. “They are very efficient, especially for the sorts of preforms used for carbonated soft drink bottles, which have thicker walls than some other types, thanks in part to their multi-stage cooling robots”. The best-in-class platen parallelism guarantees unprecedented mold life and extremely low refurbishment costs.
Stefano Baldassar also says that the complete integration of auxiliary equipment into the XForm 500 systems makes them easy to use by operators. “Plus, mold changeover is easier than with other systems, thanks to the great accessibility provided to the clamp area. This helps make moving from one mold to another quick and reliable”.