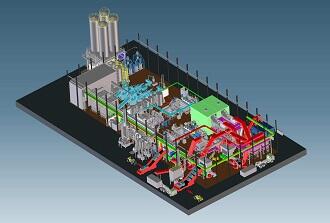
The recycling division of Amut has won two supply orders for two major European companies active in recycling plastic waste. Each order includes two twin systems for recycling and regenerating polyolefin flakes to be subsequently transformed into granulate.
In one of the projects, the twin line will work in parallel to process LDPE flakes at an hourly output rate of 2,500 kg. The flakes will come primarily from bales of post-consumer packaging bubble film. To increase system flexibility, a unit set of conveyor belts will enable two grinders to feed the two buffers on the lines alternatively. The decanting stage will separate heavy materials and film contaminants, while presorting will remove other pollutants and dirt. A second intensive rubbing action will take place during the wet regrinding stage.
The Turbo and Friction washer systems will carry out intensive and continuous cleaning and rinsing action. The process water can be thermally regulated and conditioned by chemical/detergent agents to increase the efficacy of cleaning. The flakes will be separated from the water and transferred to the centrifuge for the drying stage. A hot air system will reduce the quantity of humidity in the flakes, making the material suitable for the subsequent extrusion process.
For the other order, on the other hand, the twin post-consumer resin cleaning line will deliver a hourly output rate of 1500 or 4000 kg of LDPE film and HDPE containers respectively, ensuring the advantage of processing both light and heavy polyolefins into separate batches using the same machines. In the first decanting tank, the material will be separated from heavy objects and contaminants and then transferred to two parallel turbines for the presorting stage. The second intensive rubbing action will occur during wet regrinding. An intense cleaning action will be provided by the Friction Washer system, where the flakes are continuously subjected to energetic friction followed by a rinse stage, to further eliminate polluted residue. The cleaning of heavy plastic residue and final rinse will be completed by the decanter, a special centrifuge that also delivers intense drying action. The order also includes an extrusion system to complete the recycling process.