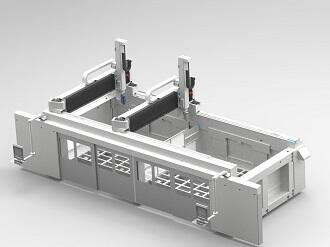
CMS SpA and Fraunhofer IWU announced their R&D partnership, focused on the development of a new hybrid system for the 3D printing and machining of thermoplastic composite parts. The new system, named CMS Kreator, will be available in several configurations and sizes, to cover a wide area of industrial needs, coming from different sectors (e.g. aerospace, automotive, marine industry, wind energy) and related to the manufacturing of prototypes and special parts.
The range of materials used by CMS Kreator is really wide: from ABS to PA and high-performance polymers, mixed with short fibre CF/GF, so as to reach 40% of fibre content, to manufacture not just mockups or jigs, but also tools and moulds able to withstand the curing operating conditions. All materials are granulate, currently used in well known industrial processes (e.g. injection moulding), easy available on the market at a much lower cost, when compared to the cost of standard FDM materials.
The extrusion is designed to get thin strands, very quickly deposited (eight times faster than standard FDM) and immediately cooled, for the building of amazing very light "bird bone" structures, obtained also by 5-axis deposition. The programming software tools are based on solutions available on the market, with the widest possibility of changing user parameters. Thanks to the multiple simultaneous operating units technology by CMS, it is also possible to provide the system with a 5-axis milling unit for the finishing and with a fibre placement unit, actually making the additive manufacturing of thermoset CFRP possible.