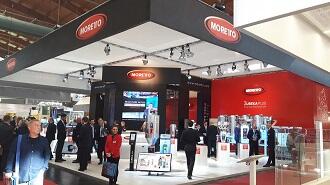
At Fakuma 2018 Moretto will be focusing on the concept of “Efficiency 4.0”, essential for the factory of the future and based on machines connected and integrated with each other by a supervision system that guarantees total control of the process. The machines can be remotely managed, they are able to supply and exchange information, to self-program and to provide frequent reports on production: all data which can be used to modify the process parameters and to monitor the performance of the machines, thus optimizing the efficiency of the entire plant.
For the connection and control of the whole automation chain in plastics processing plants, the company offers the Mowis 3 system, adapting to the needs and objectives of every customer. Based on Scada system, Mowis 3 allows a safe and immediate exchange of data between standard modules, tailor-made modules and the customer management system.
As far as dehumidification is concerned, Moretto provides solutions suitable both for complex models, such as multi hopper systems, and for the treatment of small quantities of technical materials, like the X Comb mini dryer, guaranteeing maximum efficiency and reliability thanks to the zeolite technology, the powerful turbo compressors, the exclusive OTX hopper and the dew point equalizer (up to -52 °C). The compact dryers of the X Dry Air series, equipped with a double-tower system with zeolite technology and a transparent OTX Pyrex hopper, ensure even higher performance by reaching dew point values up to -70 °C. For multi hopper plants, the Eureka Plus system is offered, reducing energy consumption by 56% and consisting of four patented technologies: X MAX, a constant performance multi-tower modular dryer; Flowmatik, a dynamic airflow management system; OTX, innovative hoppers with an exclusive internal geometry; Moisture Meter Manager, a device which measures residual moisture in-line and manages the entire drying system. Their combination makes it possible to obtain modular, automatic, self-adjusting and energy-saving drying systems.
The company also presents DPK, the new compact loss-in-weight dosing unit, suitable for intermittent or continuous dosing of small quantities of colour or without overdosing. Thanks to its vibration immunity, its control algorithm, and the hopper removable from the dosing unit, DPK achieves a dosing accuracy up to ±0,03%. Among the innovations on show there are also three new hoppers. The TM hoppers made of stainless steel and with a characteristic cone shape, guarantee an optimal material flow, and are suitable to accept single-phase or three-phase feeders and receivers for centralized conveying systems. The TMC hoppers, also manufactured in stainless steel, are used for the treatment of dried hot materials, and stand out for their double-wall insulation with removable cone. The Krystal hoppers (TMK), made of transparent shockproof acrylic material, allow the operator to immediately verify the level of material.
The new chillers of the RC Mini series, made of stainless steel, are available with cooling capacities from 6.8 to 26.2 kW, and feature a compact, space-saving design. The new RCV X Cooler modular chiller is characterised by a cooling power up to 900 kW and can be expanded up to 6 units. It consists of screw compressors with variable flow, shell and tube evaporators, large-sized condensers, channelled centrifugal fans and electronic expansion valves that guarantee a high Coefficient of Performance (COP). The X Cooler chillers are suitable even for the most demanding applications, minimizing energy consumption. Towards a refrigeration increasingly sustainable and “4.0”, Moretto’s chillers use refrigerating gases with low Global Warming Protection (GWP) and Ozone Depletion Potential (ODP) values.
Te-Ko water, oil or pressurized temperature controllers complete the range of products displayed by Moretto, together with the Dolphin distribution manifolds, the Kruise Kontrol speed control systems and the suction units with cyclone filter.