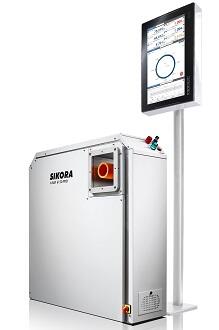
With the X-RAY measuring system X-RAY 6000 PRO from Sikora quality control of hoses and tubes is done fast and precisely, directly in the extrusion line. Within milliseconds, an X-ray image of the product is generated showing all measuring values, such as diameter, ovality, wall thickness and eccentricity. The measuring values are visualized on the monitor of the processor system Ecocontrol 6000. Sikora continuously optimizes the performance of the measurement solutions, enabling the operator to use its full potential for process optimization.
The X-RAY 6000 PRO for the measurement of multi-layered products is combined with the display and control system Ecocontrol 6000, a powerful processor system with a vertically mounted 22-inche TFT monitor, which shows the measuring values numerically as well as graphically as trend and statistical data. The wall thickness is displayed at eight measuring values as standard. Additionally, an intelligent physical evaluation model determines the minimum wall thickness, meaning the available value that optimally supports the operator to control the process. Moreover, the physical model enables the visualization of the wall thickness at any position over the total circumference of the hose or tube. For example, as an alternative to the standard display of 8 measuring values, a visualization of 12 or more measuring values is possible. The operator selects how many points and at which position the values are being displayed. Furthermore, the processor system is used for an automatic control of the line speed, respectively extruder rpm. Hence, it guarantees to comply with given specifications as well as the highest performance for a maximum of process optimization and productivity.
The X-RAY 6000 is available as an alternative to the X-RAY 6000 PRO. The measuring system focuses on single layer products. The product data is displayed on an integrated 7-inche monitor at four measuring points. In combination with an Ecocontrol 6000, 1000 or 600 processor system, a line control regarding line speed or extruder rpm can also be realized.