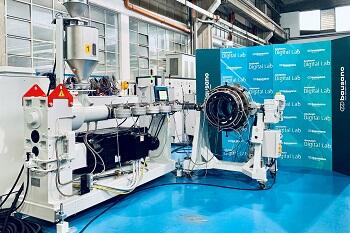
The global demand for plastic pipes has grown exponentially and, over the next few years, is set to increase for a large variety of applications: from water and gas supply networks, rainwater drainage and the transport of various fluids to energy supply systems and sprinkler systems. In this context, Bausano announces that it has completely revamped its ranges for the extrusion of soft and rigid, transparent, supercharged or press-filled PVC, PP and PE pipes in order to meet the ever-increasing demands of manufacturers for excellent melt homogeneity, flexible processes, maximised output and reduced energy consumption.
The main innovations include the launch of a new generation of extrusion heads. In particular Bausano offers a range of models for the manufacture of PVC pipes, either double (up to 110 mm) or single output (from 10 to 800 mm), for a maximum production capacity of 2,000 kg/h. As for the extrusion of polyolefin pipes, Bausano technology is designed to ensure high hourly throughput with reduced energy consumption. The heads stand out for their compact design for monolayer or multilayer production: radial spiral, ensuring better melt distribution within a smaller volume and with reduced pressure build-up, or helical spiral. These are modular systems where the number of layers can be easily increased by adding special modules. A combination of both designs, helical and radial, is also possible depending on the structure of the pipe, its materials and its dimensions. The offer also includes an internal air pipe cooling system, which cools the pipes more quickly, thus improving their quality while taking up less space when installing the line.
Bausano’s extruders also include the innovative Smart Energy System for heating the cylinder through an electromagnetic field, thus saving up to 35% on energy.
The Bausano lines also include new end-of-line accessories such as cooling and calibration benches made of stainless steel, which are crucial to the success of the whole extrusion process, with pipes that are cut to size and have a flawless surface. Specifically, the tank for PVC pipes allows for quick and accurate positioning during processing due to the three axes, which can be easily adjusted, and the motor-driven longitudinal movement. In the case of polyolefin pipes, the benches are designed to calibrate and cool a wide range of diameters between 5 and 1600 mm. Last but not least, a dual chamber configuration is available for both applications, with temperature and water level control, which allows different vacuum conditions to be created as required.
“We made the decision to upgrade our extrusion lines for PVC, PE and PP pipes as we wanted to meet the demands of manufacturers that always need to ensure that their supplies are in compliance with technical requirements, without compromising on efficiency and performance. The design of the new extrusion heads and end-of-line accessories stems from our unique ability to combine process consulting, technological expertise and a passion for innovation. Our people are the driving force behind our efforts, which have the ultimate goal of streamlining our customers’ industrial processes and ensuring the highest possible level of performance”, said Clemente Bausano, Vice President of Bausano.