Sulla nuova monoposto del PoliMi prestazioni meccaniche ed estetica grazie a Radilon Adline
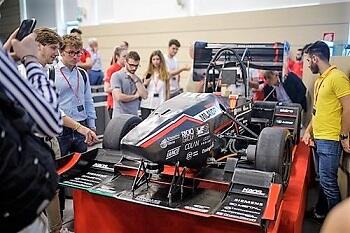
Ci sono anche i filamenti Radilon Adline sviluppati da RadiciGroup per la stampa 3D nella nuova monoposto da corsa progettata dal team Dynamics PRC del Politecnico di Milano: oltre 100 studenti di ingegneria e design hanno lavorato insieme per oltre un anno per mettere a punto una nuova vettura elettrica predisposto anche per la guida autonoma.
Ogni anno la scuderia corse Dynamis PRC del Politecnico di Milano progetta un nuovo prototipo di vettura per la Formula SAE, che compete in un campionato universitario internazionale di design ingegneristico. Nelle ultime due stagioni, il team Dynamis PRC si è classificato come migliore squadra italiana e ha raggiunto ottimi risultati a livello internazionale.
“Quest’anno il Gruppo”, ha dichiarato Angelo Radici, presidente di RadiciGroup, “ha deciso di sostenere questo progetto universitario di PoliMi in linea con la sua attenzione a supportare giovani studenti (hanno tra i 19 e i 25 anni) impegnati nel coniugare studi e attività extracurriculari, in un settore come quello dell’automotive in cui RadiciGroup ha una grande competenza in termini di materiali e applicazioni”.
“Siamo stati contattati dal team del PoliMi”, ha sottolineato Chiara Devasini, marketing & development project leader di RadiciGroup High Performance Polymers, “per capire come potevamo essere di supporto con i nostri materiali innovativi, visto che da oltre quarant’anni siamo nella supply chain dell’automotive per cui mettiamo a disposizione innumerevoli soluzioni, studiate per soddisfarne gli stringenti requisiti tecnici e, negli ultimi anni, con particolare attenzione al mondo dell’e-mobility. Dopo una serie di confronti sulle necessità dei ragazzi per il nuovo progetto, abbiamo pensato di utilizzare uno dei prodotti della nostra gamma Radilon Adline, specificatamente studiata per la tecnologia dell’additive manufacturing. Si tratta di filamenti basati su speciali gradi di poliammide che presentano caratteristiche tecniche avanzate come resistenza meccanica, chimica e termica e sono adatti non solo per la prototipazione, ma anche per la produzione di parti funzionali e strutturali come è stato in questo progetto”.
Con i materiali RadiciGroup, infatti, è stato stampato un supporto per tenere in posizione corretta il cavo motore, molto fragile, durante la sterzata della vettura e sono state prodotte delle “centine” interne all’auto, componenti essenziali per il comportamento strutturale del profilo alare in carbonio. Inoltre, grazie alla collaborazione con Ciano Shapes, distributore ufficiale dei materiali di RadiciGroup destinati alla stampa 3D che vanta un’esperienza consolidata nel loro impiego nello stampaggio, sono stati stampati prototipi di alette che si sono rivelate fondamentali per il team Dynamis per alcune valutazioni tecniche sul design del componente. Una collaborazione per sperimentare e individuare nuove soluzioni per il futuro.
“I componenti della macchina DP13”, ha spiegato Ambra Suardi, R&D scouting & consumer industrial goods project leader di RadiciGroup High Performance Polymers, “necessitavano di essere sviluppati con prodotti performanti, ma leggeri. La leggerezza della macchina è un requisito fondamentale, ma durante lo sviluppo del progetto abbiamo valutato che sia il supporto cavo motore sia le centine flap aerodinamiche sono componenti soggetti a stress meccanico. Adline CS CF10 HP BK è un prodotto specifico per l’additive manufacturing su base poliammide e rinforzato con fibra di carbonio. Di conseguenza, il grado presenta una densità tale da permettere lo sviluppo di componenti leggeri, ma altamente performanti, caratterizzati da ottima resistenza meccanica e rigidezza. Il nostro Radilon Adline CS CF10 HP BK è inoltre caratterizzato da buona processabilità in 3D printing, fattore che lo rende idoneo anche per stampanti non altamente professionali e versatile per svariate applicazioni”.