Frenare in sicurezza con Technyl Max
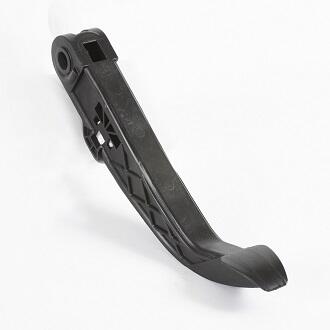
Il produttore di soluzioni per l’industria automobilistica, Carbody, ha scelto la poliammide 6.6 Technyl Max di Solvay Performance Polyamides per sviluppare il nuovo pedale del freno Skeleton totalmente in plastica.
“I costruttori automobilistici e i fornitori di primo livello stanno sempre più spesso cercando materiali ad alta rigidità per sostituire una serie di componenti metallici, al fine di alleggerire i veicoli movimentati da energie di nuovo tipo. È stata una grande opportunità per noi quella di progettare Skeleton in stretta partnership con Carbody e di dimostrare così le prestazioni del nuovissimo Technyl Max ad altissima carica”, ha commentato Gérald Durski, direttore marketing di Performance Polyamides di Solvay.
Skeleton possiede una struttura in composito a forma di barra, sovrastampata con la nuova poliammide 6.6 Technyl Max caricata al 60% con fibra di vetro. Questo fornisce al pedale del freno una maggiore resistenza alla rottura con carichi fino a 3.000 N, assicurando elevati standard di sicurezza anche al di là di questo limite, considerando che la forza media applicata in caso di emergenza arriva a circa 500 N.
“La robustezza di questo nuovo Technyl Max è stata determinante nel massimizzare la leggerezza di questo esclusivo concetto di pedale. Ci affidiamo all’esperienza pluriennale del team di Technyl nella sostituzione del metallo. La loro rinnovata piattaforma di servizi HUB by Technyl rappresenta un fondamentale strumento di differenziazione per ottimizzare la progettazione e le prestazioni di componenti essenziali per la sicurezza”, ha spiegato Loïc Lefebvre, tecnico della ricerca e sviluppo di Carbody.
Oltre ai pedali per i freni delle autovetture, Technyl Max può trovare impiego nella realizzazione di componenti semi-strutturali, come le traverse di sostegno della trasmissione e del motore, le griglie dei condotti di alimentazione e le strutture dei sedili. La sua bassa densità garantisce consente di ridurre il peso rispetto ai sistemi tradizionali realizzati in pressofusione, con livelli paragonabili di resistenza alla trazione. Questo aspetto è particolarmente importante nelle applicazioni per veicoli elettrici, che richiedono rigidità e resistenza alla fatica ancora maggiori, a causa delle frequenze più alte.