Una macchina speciale per i BMC
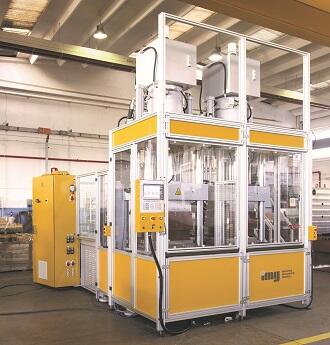
In virtù delle tantissime soluzioni ad hoc che caratterizzano la produzione di IMG, di volta in volta la casa bresciana riesce a proporre ai propri clienti - che per solito utilizzano le più diverse tecnologie di stampaggio - innovativi sistemi per l’iniezione multicomponente di termoplastici, piuttosto che originali sistemi di caricamento e iniezione del silicone liquido e/o in “pasta”, come anche particolari sistemi di caricamento e iniezione dei BMC (Bulk Moulding Compound). Proprio in quest’ultimo contesto IMG ha realizzato una macchina speciale che merita di essere descritta. Prima però, può essere utile tracciare un breve identikit dei compositi termoindurenti in massa.
Sono definiti compositi termoindurenti in massa - noti anche con l’acronimo BMC, che sta per Bulk Moulding Compound - particolari compound utilizzati nello stampaggio a compressione e a iniezione che consentono, tra l’altro, il rinforzo mediante fibre di vetro, di carbonio, minerali, o aramidiche (naturali o miste), in genere con una percentuale massima del 65%.
Le principali applicazioni dei BMC riguardano la componentistica in ambito elettrico. Più in generale l’impiego dei materiali termoindurenti - quali i BMC - è consigliato quando sono richieste buone proprietà meccaniche, ma anche in presenza di spessori variabili nelle sezioni dei prodotti. La garanzia dell’assenza di risucchi o di alterazioni delle cavità interne, come anche una stabilità dimensionale nel tempo e l’elevata resistenza alle alte temperature (contrariamente ai termoplastici) sono altre eccellenti prerogative dei termoindurenti.
“Abbiamo da poco realizzato una macchina speciale che lavora i BMC con modalità innovative, utilizzata per la fabbricazione di componenti elettrici”, esordisce Carlo Frigerio, responsabile commerciale di IMG.
Il BMC è quindi
un materiale che possiede prerogative incredibili - in primis è ignifugo - e in
vari contesti applicativi, come di seguito argomentato da Frigerio, è ormai
obbligatorio: “Dato che, in presenza di fiamme, il BMC è un materiale che non
sprigiona fumi e poiché si è scoperto - ahimè, con non poca drammaticità - come
in caso di incendio scaturito ,ad esempio,all’interno di un vagone ferroviario
ben il 50% delle vittime muoia soffocato, e non ustionato, le nostre ferrovie
delle stato hanno stabilito espressamente l’obbligatorietà dell’utilizzo dei
compositi termoindurenti in massa come materiale di supporto per taluni
componenti elettrici. Quali siano tali dispositivi non posso rivelarlo, in
quanto coperto da segreto aziendale. Posso però dire che alla base di questi c’è
una parte elettrica che viene inserita all’interno di uno stampo, per essere
poi annegata nel BMC.
E stiamo parlando di grandi spessori, che richiedono tempi lunghissimi di polimerizzazione!
Per poter ridurre il più possibile tali tempi di ciclo, IMG ha realizzato una macchina con due chiusure affiancate, ma con una sola unità d’iniezione posta sul lato opposto all’operatore, che trasla quindi da una chiusura all’altra. In tal modo, mentre è terminata la fase d’iniezione nello stampo “A” si ha tutto il tempo per traslare l’unità d’iniezione e andare - con un “ciclo pendolare” - a eseguire una seconda iniezione nello stampo “B”. Va da sé che la caratteristica più interessante di questa macchina riguarda proprio il fatto che è dotata di un solo iniettore”.
Con tale soluzione a “ciclo pendolare” i tecnologi IMG sono quindi riusciti a ridurre i tempi di polimerizzazione di più del 50%... il che non è per nulla banale.