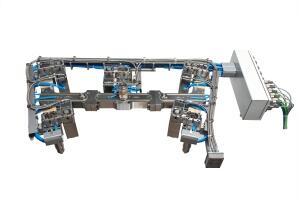
The new Flexflow electrical cylinder powered by HRSFlow makes it possible to adjust the gate pin precisely when injecting large automotive parts such as bumpers, dashboards and doors. More generally, it can be used for producing any kind of large part requiring a sequential moulding process, as well as optical components which must meet high aesthetic standards.
This system allows the gate pins to be controlled totally independently during the opening and closing processes, thus ensuring an accurate adjustment of their position, acceleration, speed and stroke. As a result, filling and packaging times can be optimised with immediate benefits in terms of part deformation control. In addition, it guarantees a high aesthetic quality is guaranteed, eliminating the most common defects such as flow marks, parting lines and flashes at the gates.
This electrical cylinder represents the ideal solution for injection moulding processes involving multi-cavity moulds and shots of different weights; it can be used whenever it is necessary to achieve precisely defined parting lines or a complex balance during the filling stage, and it meets the requirements of applications demanding tight moulding tolerances and the use of specific materials. The complete absence of oil makes it suitable for clean room operation.
Compared to conventional pneumatic or hydraulic cylinder, Flexflow offers a range of advantages, including: "A" class surfaces for automotive components; high aesthetic yield for lighting parts; improved performance for engineering materials; process repeatability; outstanding part consistency; accurate process control; weight balance optimization, minimising the risk of excessive packaging; reduced clamping force; maximum flexibility in multi-cavity moulds design; reduced energy requirement; ease of use and maintenance.
The Flexflow system is available in the M, G and A versions (with pin diameters of 5, 7 and 10 mm respectively), and is designed to operate at a maximum pressure of 2500 bars. The nozzle is located on the side of the axis, thus reducing the hot manifold height, and can be easily equipped and replaced with a hydraulic cylinder. In addition, it can be installed in three different positions, in order to ensure maximum freedom in mould design.
The full gate pin control enables the user to adjust the filling pressure in order to avoid abrupt drops: pressure drops can be avoided by controlling the gate pin opening and stroke. This makes it possible to reduce flow marks on the moulded part. The gate pin position can be set with a precision of 0.01 mm from the control unit, available in the 8, 12 and 16 zones versions.