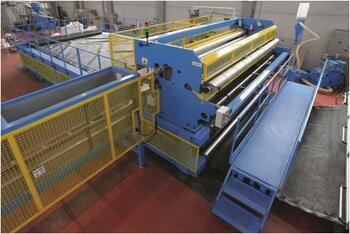
An extrusion line for HDPE dimpled membrane with net width of 4 meters has been recently manufactured by Amut for a major Russian producer of building materials. HDPE dimpled membranes are widely used for the protection and drainage of underground walls, as well as for the protection and ventilation of waterproofing layers between concrete foundations and the ground. Moreover, its versatility makes it suitable for works in areas characterised by high amounts of water.
This line grants output rates exceeding 1,700 kg/hour and allows the manufacturing of products in single reels with a width of 4,000 mm or with a central cut, in order to obtain two 2,000 mm reels or, alternatively, four 1,000 mm reels with a maximum diameter of 490 mm. The linear throughput speeds reaches 12.5 m/min, while the range of thicknesses varies from 350 to 1,000 g/sqm.
The Amut line is based on an EA 180 single-screw extruder with a 45 L/D ratio and ensures reliable production starting from granules, flakes or regrind materials obtained from post-consumer HDPE bottles, thus ensuring a homogeneous feed even in the presence of raw materials with different particle sizes. The plant consists of a loading system; a metering unit for raw materials; a single-screw extruder with a plasticising capacity exceeding 1,800 kg/hour, provided with a high-vacuum degassing system for the extraction of volatile components for the processing of materials from post-consumer bottles; non-stop oversize screen changers; a high pressure gear pump, able to process high molecular weight polymers; a flat head with a melt outlet over 4,300 mm wide and, therefore, capable of granting the maximum operating width even in case of products with a reduced thickness (less than 300 g/sqm.) Moreover, the expertise gained by the manufacturer based in Novara in thermoforming equipment has led to the development of a special calendering/forming unit. Such a width, along with the linear delivery speed requested by the customer, namely 10 m/min, actually required an in-depth study of the cooling flows in the two main forming rollers through recirculation and temperature controlling pumps, as well as a vacuum distribution system for the forming stage able to satisfy the different requirements of each finished product.
Since the line processes 100% post-consumer material, the vacuum generating unit is equipped with condensation and anti-condensate systems in order to eliminate the condensate which might pollute the melt and act as a problematic element in the vacuum circuit. Downstream the calendering/forming unit, a 4 meter wide unwinding/laminating unit for geotextile materials is installed, including a hot melt glue distribution system for the adhesion of different types of supporting/reinforcing materials. The delivery side the extrusion line consists of an automatic winder complete with a unloading/storage table for the finished product reels.
The plant is also equipped with complementary and ancillary equipment such as a bilateral unwinding system for the caution/advertising tapes directly applied in the forming step as well as a scrap grinding mill provided with a transport system for the ground material directly to the raw material loading/mixing area. A proprietary software specifically designed and developed to address the special requirements of the line controls all functions and operating parameters, in addition to storing and monitoring the production process.