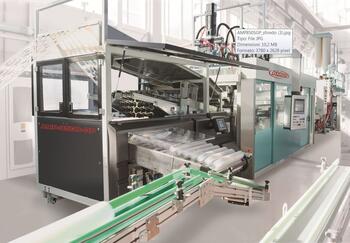
A complete in-line thermoforming system manufactured by Amut for the production of disposable cups (in the sizes required by the Usa and Canadian markets) has been successfully tested and delivered to a large North American producer. The customer's request included some very demanding features: production of disposable cups in PS and PP; use of the same lid for the cups produced in PS and PP, after the rimming, ensuring a perfect seal to the liquids; same cut diameter of 94 mm but with weight from 9 to 16 gr per piece, for all three products 12 oz, 16 oz and 22 oz. Amut has found the right solution to satisfy the requirements of the customer by developing an integrated in-line machine where all the operations are in-line, automatic and continuous, from the raw material dosing unit to the packaging of the finished product, with total in-line recovery of thermoforming scrap (skeleton).
The necessity to process both materials with the same machine resulted in the selection of a thermoforming machine with integrated forming and cutting technology and equipped with the AMP 850 GP tilting platen from the Amut Comi range. Being one of the largest and fastest machines available on the market, the AMP 850 GP ensures high outputs, over 63,000 cups per hour, using a 33-cavity mould for cups with a diameter of 94 mm. The throughput speed achieves 32 cycles per minute.
The thermoforming plant also includes a conveying system designed to handle up to 2.3 mm thick sheet and with a heating oven optimised via a dedicated management and control system specially developed for the properties of PS and PP. The performance of the mould and forming temperature control circuit has been improved and enhanced; the management of the thermodynamic cycle has been integrated and improved with a new control system. The movements are direct thanks to the high-torque motor for the plug assist unit.
The extrusion section is very important because, in particular, a sheet processing capacity of 1,300 kilos per hour is required when cups of 20 oz are in production. The line is made up of:
- 4-component feeding and dosing system; one of these components, i.e. the material from the ground skeleton, is processed in a closed loop;
- main single-screw extruder, model EA 130, complete with metering system controlled via specific software, with a plasticizing capacity up to 1,200 kilos per hour and vacuum degassing unit complete with a closed loop water management system;
- single-screw co-extruder model EA 75 for the external layers;
- continuous screen changers and melt gear pump unit both for the main extruder and coextruder;
- co-extrusion feed block suitable to make sheets with different layers configuration - A/B, BA, A/B/A - without interrupting the production process;
- extrusion die with completely automatic thickness regulation and control system;
- vertical calibration/cooling calender with rolls of 1000 mm for a homogeneous and efficient cooling of the sheet, even at maximum output speed and without inner tensions;
- gauging thickness unit and related automatic control systems of the extrusion die.
The thermoforming system can run up to a speed of 40 cycles per minute also with moulds of maximum size (850 x 560 mm), it delivers an air powered clamping force of 70 tons, and it is equipped with an advanced mechanical system for platen motions which minimises inertia and related problems.
In addition, the automated PUS stacking unit of the machine picks up the cups using a vacuum system. This unit facilitates the start-up operations and ensures high and constant efficiency in production, even when handling heavy items. The cups produced are discharged and automatically conveyed to the rimming unit that shapes the edge and accurately calibrates the outer diameter for perfect cup/lid joints. This operation is absolutely critical and is subjected to strict quality checks during production. The rimming machine has been developed to handle both PS and PP with 4 rimming screws of special design with adjustable position, with the possibility to change the rim diameter at both the entry and delivery side of the machine.
The whole system is rounded off with a packaging unit which packs the cups in rows of 20-100 pieces. This unit is also available in the “twin pack” version delivering the cups in twin rows of 50-100 pieces.