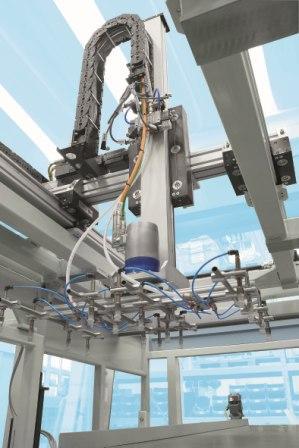
The Swiss manufacturer of thermoforming machines, WM Wrapping Machinery participated at Plast 2015 presenting the last version of the Speedmaster Plus pressure forming machine: the FC 780 E IM2 model with steel rule cutting station, fully automated counting system, and stacking robot. The Speedmaster Plus is a new generation of vacuum and pressure forming machines which assure the highest level of automation and, thanks to a new B&R control system, guarantee efficiency and higher performances with any materials. Constant forming quality, very short retooling time, accuracy in cutting, high flexibility and very ease of use are only few of the advantages of these machines.
The Speedmaster Plus machines include integrated power regeneration: the kinetic energy generated during braking movements is converted in electrical energy that is regenerated into the power system of the machine with important results in terms of energy saving. The model presented at Plast 2015 features a forming area of 780 x 570 mm, and can form and cut in the same forming station and/or in a second inline station.
The FC Speedmaster Plus thermoforming machines are fitted with two infrared ceramic heaters, upper and lower, and the adjustment of the temperatures occurs by independent longitudinal rows (upper and lower). Various partitions are available to optimize the heating in function of the material to be processed. An optical reader is also installed in order to have an automatic closed loop control of the temperature. The entire oven structure is insulated to keep heat dispersion at minimum, increasing the yield, providing further energy saving.
The forming/cutting station and the second cutting press are both equipped with two independent movable platens (upper and lower) which run along four tiebars, moved by a rod and crank system combined with a dual toggle, driven by two servomotors. A motorised vertical adjustment of upper and lower platens guarantees perfect controls of the cut height. The automatic mould locking and the adjustment of the X and Y axis are available on both platens. The X-Y movements are electrically driven and fitted with position transducers. The stacking system consists of a 3-axes robot available to solve stacking of complex shapes even with A-B-C function. The machine at the booth was displayed with a mould for APET dual valve.