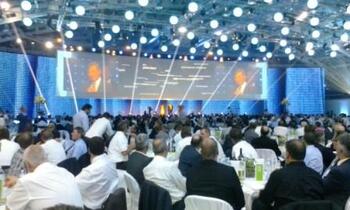
Engel's tie-bar-less technology promotes design freedom, efficient processing methods, compact production cells and creative process ideas. The Austrian company periodically honours outstanding applications with the Engel HL Award. Three companies were honoured at the design centre in Linz on the evening of June 16 during the 2015 Engel Symposium. The 2015 HL Awards went to Hengst Automotive, Gardena and Schneegans. It was the eighth time Engel recognised applications that make excellent use of the advantages of Engel's injection moulding machines with tie-bar-less clamping units. For the first time, the prizes were awarded in three categories: "Efficient use of the mould area", "Innovative process integration" and "Economical automation concept". 27 plastics processing firms from 14 countries applied for the internationally coveted distinction this year. All the applications submitted were scrutinised closely by the jury which traditionally consists of three representatives from the areas of university research, industry and the trade press. The 2015 panel included Frank Ehrig, director of the Institute for Material Engineering and Plastics Processing (IWK) at the University of Applied Sciences Rapperswil in Switzerland, Gunnar Hack, managing director of Hack Formenbau in Kirchheim unter Teck, Germany, and Harald Wollstadt, editor-in-chief of the trade magazine Plastverarbeiter.
The replacement of metals with plastics is progressing rapidly, and this also includes components under car bonnets. Hengst SE & Co, which is headquartered in Münster, Germany, has developed a thermoplastic solution made from polyamide reinforced with glass fibre for fabricating oil filter module bases that are used in various Audi and Volkswagen four-cylinder diesel engines. The filter bases are among the most sophisticated components that the automotive supplier manufactures at its production plant in Nordwalde, Germany. The single-cavity mould has altogether eight core pulls, which account for its considerable size. The bases are made on an Engel victory 3550/450 tech injection moulding machine with a clamping force of 4,500 kN. The tie-bar-less 4,500-kN machine enabled Hengst to reduce the investment and operating costs for the application considerably, keep the production cell compact and also drastically shorten the time spent for mounting and setting up the mould. The integrated ENGEL viper 40 robot can reach from the side directly into the mould area without having to circumvent any obstacles. This lowers the working height and ensures that the robot remains well clear of the heavy-duty crane in the relatively low-ceilinged production hall. It has won Hengst the 2015 ENGEL HL Award in the category "Efficient use of the mould area".
At 20 million units per year, connectors for garden hoses are the components with the highest production volume at Gardena Manufacturing in the southern German municipality of Gerstetten, a company of the Husqvarna Group. Since January of this year, an Engel victory 740H/310W/400 WP combi injection moulding machine has been used for them. Only the tie-bar-less clamping unit makes it possible to combine maximum precision with very short cycle times in the newly developed two-component process. The integrated Engel easix multi-axis robot removes 16 hose connectors from the machine every 16 seconds. In order to be able to process the thermoplastic housing material and the elastomer for the grip surfaces simultaneously, the rotary mould has two sets of 16 cavities and four sets of 16 cores. The process has an ingenious twist: after the thermoplastic components have been injection moulded, the mould then turns the cores so that they are in a cooling position before overmoulding the soft components in a third step. This prevents the cooling from extending the cycle time. When turned to the fourth position, the connectors can finally be removed from the mould. The four sets of 16 cores are each arranged in linear fashion. The heart of the tie-bar-less clamping unit, the force divider, plays an especially important role in ensuring the connectors produced in the cavities at the top and the bottom have exactly the same wall thickness as those produced in the middle cavities. Two of these central flexible elements are located behind the moving mould mounting platen and distribute the clamping force evenly across the entire mould cross section. In so doing, they guarantee very high reproducibility levels and excellent mould protection and have thus made a crucial contribution to the fact that the production cell hasn't produced any quality-related rejects since it was commissioned. Although the mould completely fills out the 4000-kN machine's mould area with its many cooling connections, there is still enough room for movement. The 2015 Engel HL Award in the "Innovative process integration" category has therefore been given to Gardena.
Space is very limited under a car bonnet. Like a big 3D puzzle, the various components needed to make the car run all have to fit together neatly. The best example of this is the oil level measurement modules. So that they fit into the space provided in the best possible way, they are no longer made of steel but completely of plastic. In addition to more design freedom, the plastic reduces the weight of the modules and also means they can be produced using a very economical manufacturing process. Schneegans Freudenberg Silicon uses projectile injection technology (PIT) to produce more than 3 million modules every year for BMW, Daimler, Volkswagen, Seat, Audi and Skoda in Losenstein, Austria. Every 45 to 50 seconds, two completely assembled units are ejected from a fully automated production cell, the core of which is a tie-bar-less Engel victory 400 tech injection moulding machine. Four integrated multi-axis robots share the tasks of inserting the projectiles, removing the moulded parts from the mould, detaching the overflow cavities, printing on the front of the funnels, fitting O-rings, assembling oil sleeves and dipsticks, leak testing and packaging the finished modules. As space is not just of particular importance under the bonnet, but also in Schneegans's production hall, a tie-bar-less solution was always going to have to be used for producing the modules. It allows the multi-axis robot supporting the injection moulding process to work especially close to the clamping unit and access the cavities without losing any time. Engel's tie-bar-less technology makes a crucial contribution to the high efficiency of the fully automated production in this application at Schneegans, and the jury has honoured this by selecting as the winner of the "Economical automation concept" category of the 2015 Engel HL Awards.