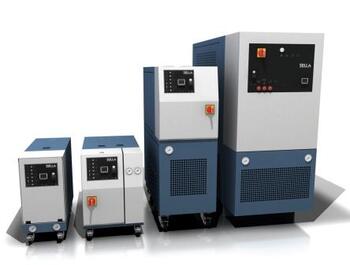
Specialists for over thirty years in the production of systems to control and adjust the temperature on industrial processes, Sella has always worked with leading Italian manufacturers of machinery and lines, including equipment for processing plastic and rubber. The best temperature control is achieved by the proper sizing of the control unit, designing the machine for the specific application. This optimizes performance and consumption of both power and fluids used for temperature control, and reduces wear on components and production scrap, boosting the overall profitability of the system.
The products that the company has recently developed, and exhibited at Plast 2015, include open and closed case temperature controllers. Open case controllers are small in size, despite which they can ensure high performance and configurability, and are suitable for small and medium sized moulds, extrusion cylinders and calenders, for tanks and mixers.
The Handy model is available in versions for water up to 90°C, from 4 to 9 kW for heating, and oil (HT) up to 150°C, from 4 to 6 kW for heating. It is fitted with immersion pumps and braze-plate heat exchangers, it functions under pressure and vacuum and supports a number of communication protocols to interface with the press or the processing line. The Handy XL model, proposed in versions for water up to 90°C, from 4 to 18 kW for heating, and oil (HT) up to 150°C, from 6 to 12 kW for heating, is fitted with 150 litre a minute high capacity pump and ensures high performance even in small spaces 230 mm in width. It is also available without temperature controller, with terminal strip commands for remote control.
The closed case temperature controllers, on the other hand, are suitable for all demanding industrial applications and have been developed for temperature control on moulds, extrusion lines, calenders, cylinders, mixers, tanks and many other applications. They are available in the S, N, L and A series, for water up to 95°C, pressurized water from 160 to 180°C and oil from 180 to 320°C, with heating from 4 to 54 kW depending on the instance, and are fitted with peripheral, centrifugal or magdrive pumps.
The S series can be installed in batteries laid side by side and can be requested also without electrical panel; the N is suitable for directly mounting on the extrusion line and is also available with air-cooling system; the L also comes in a dual zone version for controlling two separate temperature control processes; the A, lastly, stands out with its modular design and high power and is also proposed in upgraded versions with heating power that can be adjusted during the different stages.