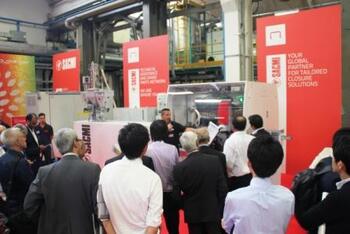
The first “Food & Beverage Plastic Day” took place on September 15 at the head offices of Sacmi in Imola (Bologna), organized by the manufacturer in order to introduce its plants and technological solutions aimed at assuring high productivity, versatility and energy savings for the beverage industry. Capable of integrating the entire process from the cap to the preform right down to the bottle, Sacmi illustrated its HERO (High Efficiency Resource Optimization) project applied to the beverage industry to around 300 guests from around the world.
The beverage industry is extremely dynamic and competitive and is continually looking for solutions capable of combining productivity and efficiency with machine flexibility and versatility in order to meet market needs in real time. All with a view to satisfying the pressing and constant need for consumption and cost optimization.
From the integration between blowing and filling and the compression presses for cap production, the manufacturer used this event as an opportunity to present the latest innovations in the IPS (Injection Preform Moulding) range, the IPS400 machine for preform production, designed to handle moulds of up to 128 cavities. This model boasts one of the lowest cycle times in the sector, and as well as incorporating the advantages of the series itself also has some winning innovative features such as the automated preform unloading system, the different circuiting within the plasticizing unit (to assure improve PET quality), as well as the particular configuration of the preform cooling stations, whereby the kinetic energy of the gripper hands is recovered during the deceleration stage and reconverted into electric energy.
Once again in this case also, Sacmi combines technological innovation with a fully integrated processing solution: Sacmi CPB Link being the new highly automated dynamic buffer that permits the integration of capsule and preform production with the bottling line, in order to achieve energy and logistics savings (HERO), while at the same time enhancing the hygiene of the process itself.
The day also focused on the latest developments of the Colora Cap system for the high-definition digital printing of caps and closure elements, which now, after years of ongoing research and development, can now also be used on coloured caps, thanks to a pre-printing system which prevents any colour alteration on non-white or transparent surfaces. Fast graphic file loading and immediate fast image change makes the system ideal for the decoration of caps for promotional campaigns and events among other things.
The latest innovations being completed with the presentation of CBF (Compression Blow Forming) technology developed for “green packaging”, that is, weight reduction at the same performance levels of containers of up to 500 ml for the dairy product sector, together with the inspection solutions developed for the various divisions, machines and plants of the group. The exhibition was rounded off with a visit to the R&D Beverage laboratory, in which solutions are developed and tested and then launched on the market.