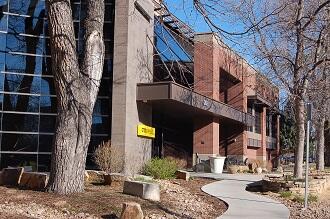
Fort Collins, Colorado. The company OtterBox, located at the foot of the Rocky Mountains, was the first to use the brand new Stratasys 3D J750 printer to produce its personalised covers for various brands of mobile phones.
Unveiled before the press at OtterBox itself on April 1st (MacPlas was there, together with around thirty other specialised journals and newspapers from all over the world), the J750 is the only printer in the world able to produce 3D objects in any colour (it has over 360 thousand colour combinations) and using various materials (up to six different polymers - from the most rigid to the most flexible, and from the most opaque to the most transparent - all printable simultaneously). The resulting objects are surprisingly realistic thanks, among other things, to the high definition/resolution of the details (up to 14 micron). The printer also allows various machines (CNC, injection moulding machines, etc.) and subsequent processes - particularly the traditional assembly of different components - to be replaced with a single, versatile production system.
After the opening words of welcome from Arita
Mattsoff, vice president of Public & Industry Analyst Relations & CSR at
Stratasys, Joshua Claman, the company’s CBO, briefly told the story of Stratasys
and Objet (whose merger was completed on 3 December 2012), illustrating various
examples from the areas of prototyping (partner company: Trek), production
tooling - thanks to Stratasys systems, Opel has managed to cut its own
production tool costs by around 90% - and components for direct use (for
example on some Airbus aircraft).
Claman, after briefly describing the various market opportunities for Stratasys printers, moved on to the day’s main topic: the unveiling of the J750 printer for 3D printing with up to six materials, and different colours and effects: soft touch, tortoiseshell, wood, transparent, and so on.
As later remarked by Roger A. Kelesoglu, sales
manager of Stratasys: “The main challenge for Stratasys today is to grant the designer
even more freedom, so that, for example, it is no longer necessary to do one
design for 3D printing and then another for industrial production, but rather
to produce a single design that can be used with both technologies. The
innovative software installed on the J750, which represents a true
technological revolution in this field, helps to make this possible”.
The previous Connex 3 (presented in 2014), with Adobe Workflow software, was already very versatile in terms of materials (up to three), colours and textures. But today, the J750, thanks to the PolyJet Studio software, is truly impressive for the realism and definition of the details: up to 14 micron, which, to be more precise, corresponds to a resolution of 600 dpi on the X axis, 600 on the Y axis and 1800 dpi on the Z axis.
Six “cartridges” located in the production
area of the J750 load as many materials, which can, in
practice, simulate any object, from chassis in imitation briar to polyurethane shoes, to give just a couple
of examples. These are advanced photopolymers, which also comprise the so-called
“digital materials”. As product marketing manager Ron Ellenbogen explained at MacPlas,
the formulas of these photopolymers (in practice, acrylic resins) are developed
in Israel, where Stratasys has its headquarters and also a chemical plant for
producing the polymers. What is more, even though they are usually associated
with rigid products, some of these acrylic resins can simulate elastomers and
silicones, as for example in the case of the “waterproof covers for mobile
phones that are currently OtterBox’s flagship
product”, declared Richardson, the man who founded Otterbox in 1998 and is now
its (visionary) president, answering questions from journalists at the end.