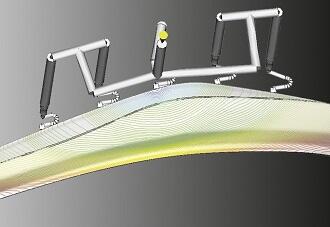
FLEXflow, the finely regulated servo-driven valve gate system from HRSflow, an INglass division, now makes it possible to carry out the series production of large-format car headlight lenses by cascade injection molding. Compared with the present standard process, it enables the part weight to be significantly reduced while maintaining the specified high quality. Especially with the cascade injection molding process, the electrically driven needle valve nozzles allow the precise, sequentially coordinated opening and closing of the valve pins with selectable velocities. This in turn permits accurate control of the melt flow in the individual hot runner nozzles and the volume flow in the cavity as a whole. With the gentle opening and shutting of the valves, the dreaded pressure loss that occurs with conventional cascade injection molding methods through the abrupt sequential switching-on of the hot runner nozzles is avoided and, with it, the accompanying marks on the molded part. In automotive construction, the FLEXflow technology has advantages in particular when injection molding large-area exterior and interior parts such as spoilers, front ends, instrument panel supports (IPS) and door liners - and now also headlamp lenses made of crystal-clear PC.
Systematic
tests were aimed, with the help of the FLEXflow hot runner technology, at
reducing the thickness - and thus also the weight - of a series-manufactured
headlight lens by lowering the amount of material required without any
sacrifice of quality. The 2.5 mm thick, 887 mm long and 120 mm wide original
lens weighing 450 g is centrally gated on the side. With the resultant laminar
flow of the melt into the cavity, the weld lines and flow lines that generally
occur with multiple gating are avoided. The test mold simulating the original
version with a glass thickness reduced to 1.8 mm was equipped with five
FLEXflow hot runner nozzles along the length of the glass. To overcome the flow
resistance of this narrow cavity, an injection pressure of well over 2,000 bar
would be necessary with a single central gating point. In the studies, the
traditional cascade injection molding method was compared with the synchronized
switching-on of the hot runner nozzles with the pin always completely open, and
the cascade injection molding process with FLEXflow control of the pin position
of the hot runner nozzles.
As expected, there are considerable problems with the traditional cascade injection molding process. The abrupt opening of the valve pin when switching over to the next injection nozzle along the flow front produces substantial pressure fluctuations when filling the mold cavity. This non-uniformity results in clearly visible optical defects (pressure marks) on the surface of the molded part, which, in the production of transparent headlamp lenses, would make them rejects.
With the precise FLEXflow control of the cascade, the pressure fluctuations on switching over the hot runner nozzles are balanced out. The cavity is filled with a uniform melt flow, as a result of which the surface of the molded part does not have any optically relevant defects. The net result are high-quality, crystal-clear headlamp lenses that can be produced reliably and reproducibly - and with a thickness of only 1.8 mm instead of 2.5 mm and a weight of only 350 g instead of 450 g.