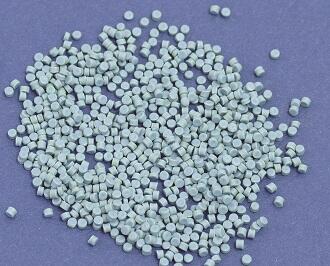
A GM125 Compac line has been supplied by Gamma Meccanica to a Turkish company for recycling of PP, PE woven and non-woven production waste. The line configuration includes the Compac feeding system with cutter-compactor, a single-screw extruder with degassing, a screen changer and a die-face pelletizer.
Like all the latest lines from Gamma Meccanica, the GM125 Compac too features a unit including extruder and feeding system assembled together, in order to offer a more integrated and space-saving configuration. The Compac feeding system is equipped with the Ecotronic system for the electronic power control, which provides significant energy savings (-40%), and allows temperature to be controlled without using water and materials with high moisture content to be recycled.
A specially designed feeding screw guarantees a steady controlled flow of material into the extruder, on which two degassing ports are installed; this facilitates the escape of gases produced during the melting of the material, thus preventing possible defects from occurring on the end product. The barrel is heated by heaters optimised for this type of application, while thermoregulation is achieved by forced ventilation, that cools the barrel when the temperature exceeds the setpoint required by the process. The exterior casing is coated with an insulating material (ceramic fiber), preventing heat loss and ensuring increased energy efficiency. The Compac’s feeding screw, together with other technical features that characterize the Gamma Meccanica recycling lines, was fundamental in the customer’s choice.
According to the company, the tests carried out on the line demonstrated its ability to produce granules of better quality and to achieve higher hourly outputs compared to the largest Italian and foreign competitors. In fact, the line produces about 10% more than competitors' lines of the same size and in a more constant way.