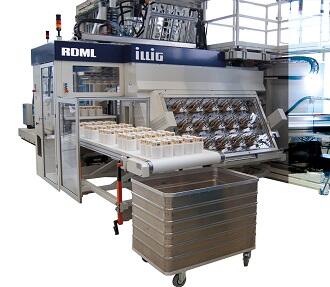
At K 2016 in Düsseldorf Illig showcased for the first time in its latest stage of development the IML-T production line IC-RDM 70K together with the compact IML unit RDML 70b for flexible decoration of almost every cup geometry. An IC-RDM 70K automatic roll-fed machine, forming area 680 mm x 300 mm, with RDML 70b IML unit, illustrated the IML-T technology.
The 18-cavity tool has an hourly output of approximately 17,280 rectangular polypropylene cups. They are decorated in brilliant photo quality on all four side walls and the bottom directly during forming. A specifically designed IML unit removes the printed blanks (labels) from a magazine and places them in the mould cavities in the forming station of the thermoforming machine. During the subsequent forming process the label bonds true to contour and permanently with the part wall. Principally, the pack can be designed without limitations, from cup-shaped through to tray-shaped. The large decoration area is a special benefit provided by IML-T technology. Moreover, the label can even add to increased pack rigidity, subject to geometry and quality. Consequently, the thickness of the material used can be reduced (saving of material costs) and still the required top load of the pack is maintained. A further benefit provided by the IML-T technology developed by Illig is the fact that every mould cavity can be equipped with an individually printed label, and a label change can be performed fast and with only low effort. All standard materials, such as PS and PP labels through to paper labels, can be processed. Cleanly separable packs can be realized.
Machines of the RDM-K series are designed specifically for economical production of cups of different sizes and shapes out of thermoplastic material. Frequently they are employed as in-line systems with upstream extruder, e.g. for large-volume production of drinking cups in millions of numbers. The machines are equipped with the IC concept (Illig Intelligent Control Concept), so the high capacity of these servo-driven thermoforming machines can be utilized easily, reliably and fast to the full extent.
Illig IML-T technology is also integrated in form, fill and seal lines (FFS lines) especially in the dairy industry. The great variability provided by the system allows synchronous filling and packing of product families. Product changes can be performed fast and with only low effort. Thanks to multi-lane equipment of the FSL 48, product families can be filled, i.e. different flavours with corresponding labels.