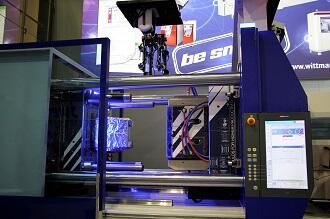
Over the last three years, Italy has developed into one of the most important markets for the Wittmann Group in Europe. This is why the Plast 2018 in Milan is also an important platform for the company (hall 22, stand B121-C122) to showcase innovative machinery and processes.
In the area of injection moulding machines, Wittmann Battenfeld exhibits at this year’s Plast one example of each machine series from its PowerSeries range in combination with interesting technologies and processes. All machines on display are equipped with the new Unilog B8 control system running under the Windows 10 IoT operating system which, compared to its predecessor version, offers a large number of additional functions and even more operating comfort. The Wittmann solution for Industry 4.0, known by the name of Wittmann 4.0, and its special features are also demonstrated to visitors on impressive examples.
To demonstrate its multi-component technology, Wittmann Battenfeld presents an application with liquid silicone. On a SmartPower 120/525H/130L Combimould, a 2-component medical part will be produced, in which one component is a thermoplastic material, the other liquid silicone. The parts will be manufactured with a 4+4-cavity mold supplied by the Italian company Silital (Oldrati group), produced by Linea Stampi. The parts are removed and deposited on a conveyor belt by a W921 robot from Wittmann, equipped with the new R9 control system.
The second application presented at the Plast shows the Airmould internal gas pressure process developed by Wittmann Battenfeld. On an EcoPower 160/750 equipped with an insider cell, a coat hanger is manufactured with a single-cavity mold from Haidlmair, Austria, using the Airmould process, whose interface is also integrated in the Unilog B8 control system. The combined compressor and nitrogen generator unit used has also been developed and manufactured by Wittmann Battenfeld. The parts are removed and deposited on the conveyor belt integrated in the production cell by a W918 robot with the new R9 robot control system.
Smart Production with individualization and
traceability according to the Industry 4.0 concept is demonstrated on a fully
automated and integrated large machine from the MacroPower series. On a MacroPower
500/3400 an attractive TPE shopping bag will be produced with a mold supplied
by Haidlmair, Austria, which can be provided with a personalized imprint. At a
terminal, all visitors can enter their names. To collect the bag with the personalized
imprint, each visitor receives a printed voucher with a QR code, which can then
be read in at the delivery station. After the QR code has been scanned in, the
next bag produced will be separated and transferred to a station where it is
laser-printed. After the fair, the production data of the “personalized bag”
can still be retrieved by scanning the QR code for another fortnight. Handling
of the bags will be effected by a Wittmann W843 pro robot equipped with the R8
control system.
To illustrate the integration of robots and peripheral appliances into the Unilog B8 machine control system, an interactive display board is also exhibited at Plast 2018, which allows visitors to test the advantages of Wittmann 4.0 themselves.
Automation and peripheral appliances
Apart from the robots and peripherals incorporated in
the injection moulding machines, Wittmann Battenfeld also presents a wide range
of peripheral appliances as stand-alone solutions.
The Plast 2018 also serves as an important platform to
present the large number of new Wittmann robot models. In addition to the
robots integrated in the production cells, the following new appliances are
showcased for the Italian market: the small Primus 14 model with an unbeatable
price/performance ratio, specially designed for the automation of small
machines; the bestseller W918 with 6 kg load capacity and the new R9 control
system; the robot models WX143 with 15 kg load capacity and the large WX163
with 45 kg load capacity are also on display at the booth.
All robots with R9 control systems are equipped with
servo-driven A/C and/or B/C axes. The R9 control system features some new
visualization options, an integrated “digital twin” for easy and safe testing
of sequences, a display panel, now enlarged to 10.1” with multi-touch
attributes, and special step keys for machine setting. The R9 teachbox still
offers the well-known programming help functions such as TextEditor, QuickEdit
and the wizard for automatic programming. This ensures full backward
compatibility with existing older Wittmann control systems.
The peripherals to be shown at the Plast Milan include the temperature controller models Tempro basic C and TEMPRO plus D. On an interactive display, the functionality of the frequency-controlled temperature controllers Tempro plus D SpeedDrive with the intelligent Flowcon plus flow controller are illustrated. The interaction and automatic adjustment of the flow quantity and the motor speed of the pump are clearly demonstrated, whenever there are any changes in the cooling channels or the operator alters the set temperature level.
Moreover, the Drymax primus E dryers are shown at
Plast 2018, each equipped with two
desiccant cartridges, which deliver a continuous supply of process air and
consistent drying air quality for perfect drying of plastic granulate, as well
as a Gravimax G14 gravimetric blender, with high-precision, wear-resistant
stainless steel valves used for metering, and a Dosimax MC Basic volumetric
blender. Furthermore, material loaders from the Feedmax plus G and Feedmax B
series with teachbox will be on display. The range will be rounded off by a Codemax
coupling station for error-free material distribution to the processing
machines and an M7.3 demo control system for the central material transport
system.
Finally, two models from the granulator range of the Wittmann Group are also on show: a Minor 2 screenless beside-the press granulator and a G-Max 12 grinder. The G-max granulators run efficiently with low energy consumption and modest space requirements. They come with a sound-insulated cutting chamber, which minimizes their noise emission.