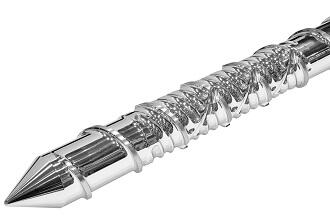
Custom-designed Xaloy screw and barrel packages from Nordson Corporation withstand the corrosive effects of fluoropolymers in the extrusion of insulation for wire and cable while meeting the processing requirements of materials as different as fluorinated ethylene-propylene (FEP) and polyvinylidene fluoride (PVDF).
Fluoropolymers are among the most corrosive materials for processing in standard extrusion systems. The screw and barrel packages now offered by Nordson include highly corrosion-resistant materials for all components, along with custom-designed screws to meet the differing processing temperatures of FEP and PVDF and the special mixing requirements of the individual customer.
The corrosion-resistant materials specified for FEP screws include Inconel nickel-chromium alloys for the base metal and Colmonoy nickel-based alloys for the hard surfacing that is welded onto the wear surfaces, or lands, of the screw flights. For PVDF screws, the recommended base metal is chrome-plated 4140 HT alloy steel or stainless steel. The barrel that Nordson recommends for use with both screws is lined with Xaloy X-800, a highly corrosion- and abrasion-resistant nickel-based alloy with tungsten carbide; for discharge flanges and feed ports, the material is Inconel.
An important difference between the two fluoropolymers is melt temperature: 230 to 290° C for PVDF, versus 360 to 380° C for FEP. This is a determinant of screw design for applications requiring mixing of the polymer with additives, modifiers, and colorants. For FEP, Nordson recommends a screw with the Xaloy Stratablend II mixer, which provides both distributive and dispersive mixing with relatively low shear. This is also recommended for mixing PVDF, but in addition Nordson also specifies the Xaloy Efficient barrier screw. The barrier screw design separates the already melting resin from solid material that has yet to melt, preventing over-shearing of the already melted PVDF and keeping the melt temperature of the overall extrudate low. Other design specifications for screws to process these fluoropolymers involve the length of the feed and transition sections of the screw and the compression ratio.
“While there is growing demand for fluoropolymers in wire and cable because of their extreme heat and chemical resistance, these materials do require plasticating systems that resist corrosion,” said Walter Smith, senior extrusion application engineer. “In consultation with customers in the wire and cable industry, we have designed package systems for FEP and PVDF that meet this requirement as well as addressing the special processing characteristics of each polymer.”