Testing screen changers together with customers
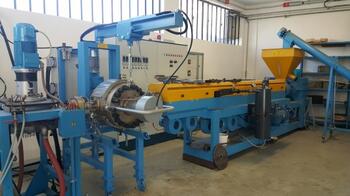
The manufacturer of automatic screen changers Fimic has set up an internal laboratory for performing specific tests. The structure is equipped with a single-screw extruder featuring a diameter of 125 mm, provided with a RAS 400 screen, venting system and vertical die-face pelletizer, and reaching an average output of up to 500 kg/h, based on the material processed.
Until a few years ago – as can be read in a note issued by the manufacturer – the ability to perform preliminary tests at plants and equipment suppliers’ facilities was rarely required, while today customers are ever more interested in checking in advance the effectiveness of their process as well as the quality of end products.
Though the extrusion line running in the laboratory is a reconditioned one that does not incorporate the latest technologies available in the recycling sector, such as a venting system mounted downstream of the screen or an underwater die-face pelletiser, it however provides information which could turn out to be useful to users. This seems to be demonstrated by the number of tests performed: approximately two per month.
Each test normally takes a whole afternoon, during which the screen changer, with a diameter of 400 mm, is opened in about 10-15 minutes, subjected to an inspection and control of its internal components, and then closed again. The product obtained after the filtering and pelletizing processes is then verified immediately, by means of a small lab extruder. Based on the results and overall data provided, it is finally possible to develop the most suitable plant layout according to the specific production needs.