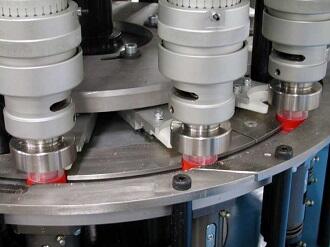
Lo studio e il miglioramento continuo dei componenti realizzati in materiali plastici sono alla base del lavoro quotidiano di progettisti e designer. L’obiettivo finale, quando si pensa a lanciare un nuovo prodotto sul mercato, è sempre lo stesso e ogni volta rappresenta una sfida: presentare un articolo moderno e il più possibile funzionale, con un occhio particolare all’estetica per incontrare anche il gradimento del più esigente tra i consumatori.
È proprio nel mezzo di questo difficile percorso che, talvolta, la collaborazione tra produttore e fornitore dello stampo diventa una condizione essenziale per concludere nel miglior modo possibile il processo di sviluppo del componente. Ed è in questa fase così delicata che Gefit si conferma uno dei costruttori di stampi per termoplastici in grado di assecondare tale condizione.
L’azienda di Fubine, in provincia di Alessandria, ormai da diversi anni, ha sviluppato un approccio totalmente innovativo che parte proprio dallo studio analitico dei componenti plastici per supportare il trasformatore nella fase di personalizzazione del suo prodotto. Grazie a un team altamente specializzato, ogni nuovo progetto che nasce in casa Gefit passa attraverso una particolareggiata analisi di moldflow, per studiare le particolarità e i possibili problemi che potrebbero verificarsi durante il processo di stampaggio.
Il vantaggio di questo approccio particolarmente analitico è semplice ma fondamentale: verificare che il componente generato dallo stampo sia effettivamente conforme a quanto desidera ottenere il trasformatore e, soprattutto, anticipare eventuali criticità che in genere appaiono soltanto in fase di collaudo. E in quel momento è quasi sempre troppo tardi per intervenire.
Fanno parte di questo processo, che accompagna passo dopo passo tutta la fase di progettazione, la simulazione dinamica, per studiare il comportamento del componente in fase di estrazione, e, ovviamente, l’analisi Fmea, per esaminare ogni possibile, potenziale rischio in chiave futura.
Ogni stampo Gefit è progettato in 3D, compresi i canali di raffreddamento, che hanno un ruolo fondamentale per determinare il tempo ciclo finale e a ogni singolo componente in acciaio dello stampo viene assegnato un codice specifico e unico, così da garantire precisione nei controlli dimensionali, qualità nelle lavorazioni e tracciabilità per il cliente.