The first industrial 3D printer for silicones
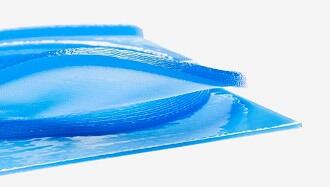
The Munich-based chemical company, Wacker, has showcased a world first at K 2016: the first industrial 3D printer for silicones. The high-tech device is called Aceo Imagine Series K, and represents the first printer generation for industrial purposes. The Aceo Imagine Series K prints considerably faster and is more compact in design. “The printer is based on the Aceo technology - a drop-on-demand method developed by Wacker”, says Bernd Pachaly, head of Wacker’s silicones research and responsible for the Aceo team. “It can be used to make parts and assemblies with complex geometries, as well as “impossible products”, which could not previously be produced”.
The term “additive manufacturing”, better known as 3D printing, describes a manufacturing process in which a workpiece is built up in successive layers, without the use of a mould - i.e., it is a mould-free process. This offers designers significantly more latitude than conventional manufacturing methods. Once a product design has been generated by computer-aided design (CAD) or imaging techniques, printing can commence immediately.
“The automotive and aerospace industries are currently the main customer sectors for 3D”, says Pachaly, who started developing a system solution for 3D printing with silicones with his team in 2014. At the moment, additive manufacturing is growing rapidly in medical applications. Biomodeling and customized geometries are particularly promising. “In these types of applications, silicones can display their favourable properties particularly well”, emphasizes the research head. “Silicones are heat resistant, flexible at low temperatures, transparent and biocompatible. They can furthermore be pigmented in any colour and have good damping properties”.
With Aceo Imagine Series K, prototypes or small series can be produced quickly and efficiently. The new 3D printing process thus offers product designers fascinating possibilities.
Aceo technology
uses a drop-on-demand method. The printer head deposits tiny silicone droplets
on a substrate. In this way, the workpiece is built up layer by layer. The
silicone is formulated so that the droplets flow together before the curing
process begins, which is activated by UV light. The droplets and layers thus
produce a homogeneous workpiece, which does not differ much from injection-moulded
parts. With the aid of water-soluble support materials, it is also possible to
create overhang materials and internal lattices.