Injection moulding and cooling cycle: how to solve common issues?
In the injection moulding process, the cooling cycle makes up to 80% of the production time. Problems such as scale fouling, rusting or slime formation in the cooling circuit of a mould only lengthen the cooling time, up to three times the optimal cooling time. In practice, this causes a 66% loss in productivity.
These data highlight how important it is to adopt proper prevention in the mould's hydraulic circuit. A critical issue that significantly impacts the production cycle, such as the quality of the water used in the plant and/or its proper chemical treatment, can be solved through essential expedients such as the use of specific filters to collect sludge combined with a magnetic sludge removal filter.
These are all measures that enable proper mould operation, reducing maintenance time and costs. Not only that, an intact cooling circuit ensures a faster production cycle and less production waste. In addition, the often associated temperature controller is more efficient and less prone to breakage.
Cooling cycle: the most common issues
In the injection moulding process, plastic material is melted and injected inside a closed mould whose cavity gives shape to the part and which opens when the part, as it cools, solidifies. The mould's cooling system must be designed with great care to allow proper water circulation within it and to allow uniform cooling of the moulded part.
"An efficient system not only ensures consistent production and waste reduction, but also contributes to better product quality in terms of surface gloss, homogeneous crystallinity of the plastic material, and reduction of internal stresses that would lead to deformation of the moulded component," explains Roberto De Col, product manager at Piovan, a world leader in the development and production of automation systems for the storage, conveying and processing of polymers and plastic and food powders.
However, this process can be compromised by several issues, such as scale, rust, and slime, which negatively affect the thermal conductivity between mould and polymer. "Limescale is the result of the reaction between carbonates dissolved in water and calcium ions, and is caused by the hardness and alkalinity of the water used in the circuit. In addition, the presence of suspended substances in the coolant can promote its formation. On the other hand, oxidation of steel, due to naturally dissolved oxygen in the water and the salts present, promotes the formation of various types of rust, including magnetite. Limestone, suspended particles and rust contribute to scale formation."
Slime, on the other hand, consists of organic substances (bacteria, algae, fungi) that develop mainly at low temperatures, around 30 to 40 degrees Celsius. Their accumulation forms a slime that clogs the cooling circuit.
"A single millimetre of sludge and fouling deposit in the cooling circuit significantly reduces the mould's thermal conductivity. Let me give an example: where 10 seconds of cooling time is needed under normal conditions, a 2-millimeter deposit requires 28 seconds," Roberto De Col further explains.
The solution: temperature controller and magnetic sludge removal filter
We have seen how a seemingly trivial issue becomes an extremely impactful problem for moulders. How to solve it? The first tip, of course, is to use properly treated water. But this expedient alone is not enough. "When we design an injection moulding system, we have to rely on a good temperature controller. We need a reliable, precise and robust machine whose function is to control the water temperature while ensuring efficiency in heat exchange." Piovan, already a market leader in the production of these machines, has expanded and evolved its offerings with the Easytherm line, a series of particularly compact and extremely reliable machines with a wide range of options and pumps that allow customers to find the most suitable solution for thermoregulating their moulds.
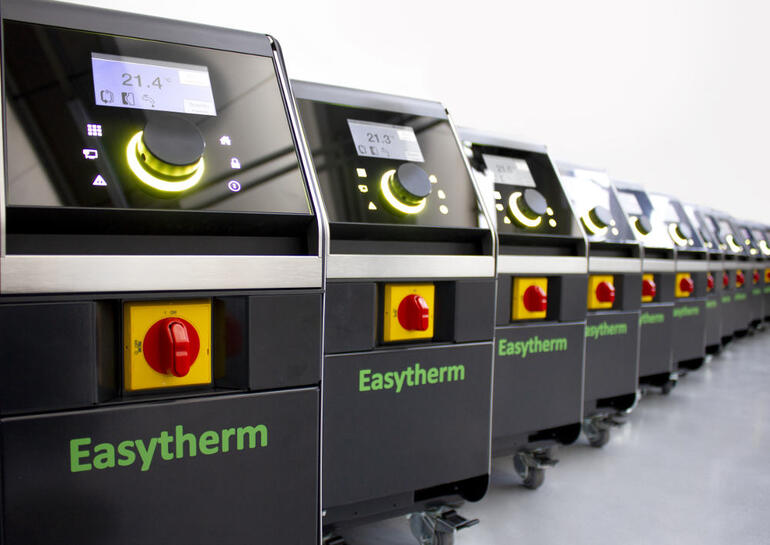
"It is essential to combine the temperature controller with a magnetic sludge removal filter, which reduces the presence of metallic or ferro-magnetic particles by blocking them in its filter." This is a T-shaped stainless steel cylinder with a mesh filter inside (usually 50 microns, but it is possible to equip the magnetic sludge removal filter with finer or wider mesh filters, as needed) and a neodymium magnet-the most powerful type on the market. The magnetic sludge removal filter is mounted at the mold return, before the temperature controller, thus intercepting all ferromagnetic substances before they reach the latter. "This allows, on the one hand, to keep the water circuit clean, and on the other, to preserve the temperature controller," adds Roberto De Col.
Simple to install, even in situations of limited space, easy to clean for very fast maintenance, it also has among its advantages total retrofittability. In fact, it can be inserted into the system together with the temperature controller, or at a later time. With significant benefits. "I remember the case of a customer with several temperature controllers installed but major fouling problems inside the mould. At the inspection, our service department immediately sensed the problem and proposed that the customer install a test magnetic sludge removal filter. Within 24 hours it cleaned up the circuit, capturing a significant mass of magnetite, which was in fact severely limiting the efficiency of the temperature controller. The customer thus decided to match each temperature controller with a magnetic sludge removal filter.”
The magnetic sludge removal filter as it turns out is a passive, non-power-consuming tool with great effect in an injection moulding system. All to the benefit of yield, quality in production and durability of other components.
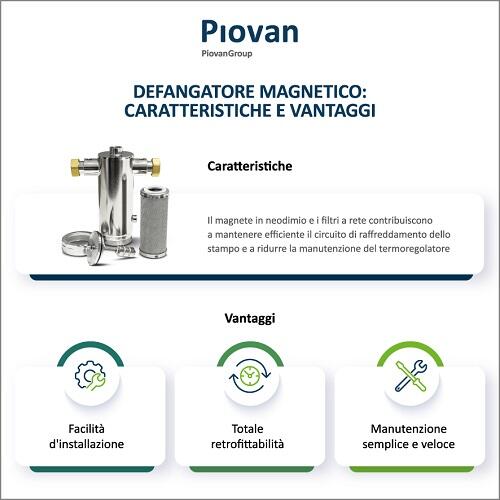
For any information: https://www.piovan.com/contacts/
Note for the Press
PiovanGroup is a global leader in the development and manufacturing of automation systems for the storage, conveying and processing of polymers, bio-resins, recycled plastic, food fluids, food and non-food powders. Over recent years, the Group has been particularly engaged in developing and producing automation systems for production processes for the bio-economies and circular economies for recycling and reusing plastic and for the production of plastics which are naturally compostable, tapping into crosselling opportunities.
Since October 2018, Piovan S.p.A. has been listed on the Italian Stock Exchange in the STAR segment. With 90 years of experience, more than 2,000 employees in 14 production facilities and 40+ service and sales branches/offices worldwide, the Group is close to its customers on a global basis, also through the continuous innovation of the solutions developed and the constant support that, starting from the design phase of the systems, extends to their installation and start-up as well as their operation. LTM revenues as at September 2023 reached EUR 567 million.