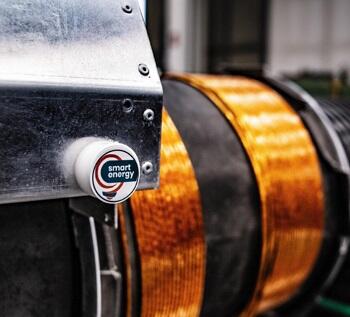
The K 2022 show is the perfect setting chosen by Bausano to introduce industry professionals to the increasingly high-performing Smart Energy System for cylinder induction heating, which helps to reduce energy consumption significantly. The system will be on display at the stand on both a twin-screw extruder from the Nextmover range and on the new single screw extruder E-GO R, designed for recycling plastics.
More precisely, the Smart Energy System designed by Bausano features forced-cooled induction coils with special openings that allow air to pass through and the temperature sensor to be installed. The coil is wrapped in highly insulating materials to minimise heat loss from the cylinder to the outside. Moreover, thanks to its innovative internal design, the cooling airflow is channelled directly onto the plasticising cylinder for faster cooling compared to resistive systems. These features can be summed up as follows: even heat distribution and lower coil surface temperature; quick heating up to 250°C; extremely accurate temperature control thanks to reduced thermal inertia.
Specifically, the Nextmover extruder, equipped with Smart Energy System, will be on display at the trade fair, along with a double output head for pipes manufacturing PVC pipes. Bausano intends to show visitors how, thanks to its technology, the overall productivity of 2,000 kg/h can be achieved for diameters from 63 mm to 160 mm while saving 35% energy.
Other essential factors for the success of the entire process are the cooling and calibration benches, made of stainless steel for pipes that are cut perfectly to size and have a flawless surface. Specifically, the line with a double output head, showcased at K in its complete configuration, has two 9 m dual-chamber parallel calibration benches with temperature and water level control, which allows for creating different vacuum conditions as required. In addition, the high-performance pipe cooling system cools the pipes more quickly, thus improving their quality and taking up less space when installing the line.
On the other hand, thanks to the 4.0 control system covering the entire line, Digital Extruder Control, with a 21-inch screen, the consumption during each stage of the process can be accurately monitored. The real-time performance display enables intervention to manage motor power, temperature, oil control unit inspection, screw adjustment and other parameters on request. Furthermore, the line meets the smart factory vertical integration requirements, allowing communication with third-party systems, such as the sophisticated in-line measurement tool to accurately check the pipe's internal and external diameter and wall thickness.
Ultimately, K will be an opportunity to launch, for the first time in Europe, the groundbreaking E-GO R technology, which can be used to feed highly contaminated plastics back into production processes. Some examples are HDPE waste from containers for milk, motor oil, shampoos and conditioners, soap, detergents, and bleach. Other applications include PP waste from lunch boxes, yoghurt pots, syrup and medicine bottles, caps and LDPE waste from cling film, shopping bags, and squeezable bottles.
“The expansion of the extrusion lines for PVC and PO pipes and for recycling plastics is the result of our unique ability to combine process consultancy, a passion for innovation and technological expertise. In this regard, throughout the event, our clients will have the chance to get to know our new team of experts in the Technical Department, who have specific skills and extensive know-how when it comes to designing these types of solutions. Innovations in the production of granules, which has always been one of Bausano’s strengths, will also be showcased. The company’s goal is to meet the needs of plastics manufacturers by combining turnkey, highly customisable systems with top-notch customer service”, Clemente Bausano, Vice President of Bausano, said.