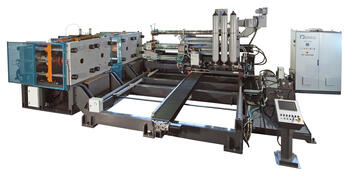
Presma recently delivered its MS 4-250-6000, featuring four linearly arranged stations, to a manufacturer of road safety products. This model is characterized by the arrangement of its mould-holder stations: unlike traditional rotary machines, here they are in-line arranged. The machine features four 2,500 kN fixed stations with a 6,600 cc translating injection unit specific for the moulding of traffic cones made of recycled PVC obtained from electrical cable insulation. The machine can produce approximately 1,000 pieces having an average weight of <st1:metricconverter w:st="on" productid="5 kg">5 kg in 12 hours. The configuration was agreed with the customer both for reasons of space and also because the machine will principally be used to produce thin-walled articles, which do not require long cooling times but do benefit from flexibility in mould changing without having to stop line operation.
This “modular” press is equipped with latest-generation drives and particular attention was dedicated to finding the right balance between electrical and hydraulic actuators, achieving a high level of energy efficiency. The injection unit is moved by means of a digitally controlled screw mechanism with “absolute” retroaction, ensuring fast and smooth operation and the perfect alignment of the nozzle in the four positioning stages at the mould. In order to reduce injection times, a “transfert” injection unit was chosen with a double punch, which makes it possible to load the volumes necessary to fill the moulds on an alternating basis and thus allows virtually continuous operation of the screw.