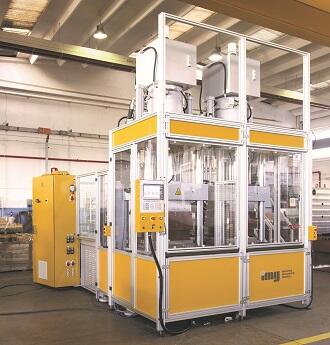
Thanks to the many bespoke solutions that characterise its production, the Brescia-based company IMG is always able to offer its customers, which tend to use the most diverse moulding technologies, innovative systems for multi-component injection moulding of thermoplastics, original systems for loading and injecting silicone, in liquid and/or "paste" form, as well as special systems for loading and injecting bulk moulding compounds (BMC). For this last application IMG has, in fact, created a special machine that it is worth describing here. First, though, it is useful to take a quick look at what these compounds are.
Bulk moulding compounds, or BMCs, are special compounds used in compression and injection moulding. One of their features is that they can be reinforced through the addition of glass, carbon, mineral or aramid (natural or mixed) fibers, typically in percentages of up to 65%.
BMCs are used mainly in electrical applications. Generally speaking, the use of thermosetting materials, like BMCs, is recommended when there is a need for good mechanical properties, but also when different product sections show different thicknesses. The guaranteed absence of sinks and internal cavity alterations, as well as the dimensional stability over time and high resistance to high temperatures (contrary to what is seen with thermoplastics) are other excellent features of thermosets.
“We have recently produced a special machine, used in the manufacture of electrical components, that processes BMCs in an innovative way”, begins Carlo Frigerio, sales director at IMG.
BMCs are
thus materials with some remarkable properties - first of all, they are fire
retardant - and in various application settings their use has become
compulsory, as Frigerio goes on to explain: “Given that BMCs are materials that
do not give off fumes in the presence of flames, and since it has been
discovered – in dramatic circumstances sadly - that as many as 50% of the
deaths resulting from a fire starting, for example, inside a carriage will be
caused by suffocation and not by burns, our national railway company has made it obligatory to use
BMCs as the material for the supports for certain electrical components. I am
not at liberty to say what these applications are, as this information is currently
a business secret. What I can say, however, is that basically an electrical
part is inserted into a mould and then embedded into BMC.
And we are talking about considerable thicknesses that require very long curing times!
In order to reduce, as far as possible, these cycle times, IMG has created a machine with to twin clamping units, but only one injection unit that, positioned on the far side from the operator, moves from one clamping unit to the other. In this way, once the injection of material into mould “A” is complete, there is plenty of time to move the injection unit across, like a shuttle, so that it can perform a second injection into mould “B”. Obviously the most interesting aspect of this machine is precisely the fact that it is equipped with only one injector”.
Thanks to this “shuttle cycle” solution, IMG’s technicians have managed to reduce the curing times by more than 50%, which is no mean feat.