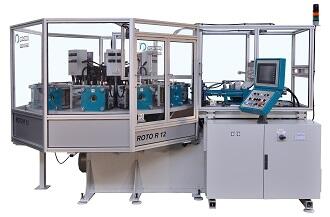
The “rotary” presses by Presma are multi-station solutions destined to the injection moulding of thermoplastic foam and thermosetting rubber. At the last edition of the K trade fair, in Düsseldorf, the Italian company exhibited the two models Roto T4/48 XL and Roto R 12.
The first one is an example of the range of special rotary machines for the processing of thermoplastic foam and has been specifically developed for the production of bottle caps. This machine was fitted with 48+48 double-cavity mould platens and four injector units, which makes it possible to produce 4 different cap models in 4 different colours/materials.
In the “transfer” injection unit the plasticisation screw and the plunger are respectively operated by an inverter controlled electric motor and a hydraulic piston. The Roto Logic control system, developed in-house by Presma, makes it possible to set different metering quantities for one or more single-cavity moulds, and to therefore produce various kinds of caps for each unit, and to test one or more moulds for caps of various shape and weight. There is a touchscreen interface for the monitoring and management of all moulding parameters, thanks to a series of sensors and alarms with cycle resetting in the case of a blockage.
This press range has been developed in order to assure the maximum production flexibility and the model displayed at K 2016 featured an automated systems which made it possible to use the different injection units for the automatic production of two-colour caps.
On the other hand, the Roto R 12 machine has been
conceived for rubber moulding in a more efficient manner as compared to the
traditional single-mould press. It can make use of twelve different moulds and
so the press can assure an assorted production, even using two different blends
in the case of the dual injection unit version. Furthermore in the event of the
use of expensive blends, the use of small-size moulds and cavities means that
it is possible to improve the quality of the items produced and to reduce the
amount of waste in the form of flash and sprue.