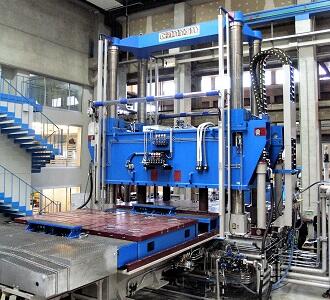
An Italian leading manufacturer of structural parts and components in advanced composite materials for the automotive and aerospace industries, Riba Composites invested recently in a new Cannon production plant for HP-RTM (High Pressure Resin Transfer Molding) and press moulding technology. Specialised in autoclave and vacuum bags/oven productions for composite parts destined to niche markets, the Faenza-based Riba Composites company needed to expand their presence in the automotive and aerospace industry. The production series and the unit prices common for the car industry being not compatible with the existing production equipment, the company decided to explore the possibilities offered today by high-productivity technologies such as HP-RTM press moulding. Cannon Ergos was consulted, with other leading suppliers of this kind of equipment, and was awarded with the supply of a complete production solution.
The Cannon solution included the machines required for high-productivity manufacture of composites using the HP-RTM process with epoxy resin matrix and carbon fibre reinforcement:
- a three-components E-System high-pressure dosing unit for epoxy formulations, with one LN 10 three component mixing head and closed-loop control of output and ratio
- a short-stroke press with 25,000 kN clamping force, 3.6 by 2.4 m platens and a very precise active control of parallelism for guaranteed planarity of the moulded parts.
Two lower platens shuttling on the front and rear sides of the press allow for an ergonomic and precise service (part demoulding, visual inspection of mould and cleaning, positioning of carbon fibre layers) on a lower mould-half while another is curing a moulded part, closed in the press.
Cure time
for HP-RTM parts can vary, increasing the mould temperatures, from 180 to 90
seconds, while injections are typically performed in less than 30 seconds, with
a trend to reduce both values to increase productivity. The two-shuttle press
design allows for a substantially higher efficiency, since the press is closed
for most of the time, while one or two operators attend the service functions
in the same time requested by the “press closing-resin injection-curing” sequence
of operations.
Through this advanced working island for HP-RTM this Italian producer, a very qualified manufacturer of high-end composites for niche market applications, is now ready to enter in the very competitive arena of tier one suppliers of CFRP parts for the automotive industry. Cannon, being able to supply all the required technologies and equipment with a “single responsibility” contract, provides a one-stop-shop approach to the companies that decide to invest in complete manufacturing solutions for composites.