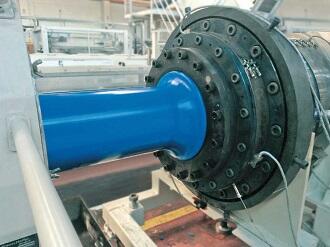
The German-based Conextru designs and builds cross heads for any kind of pipe coating application, from bundling of small pipes for optical fibres to coating multilayer structures with barrier layer for small pipes, like those used for floor heating, as well as for large pipes, like water transportation pipes, through to single layer coatings as protection layers for handling pipes during installation. Cross dies are a preferred alternative to produce the jacket of pre-isolated pipes for in line processes. The diameter of such heads can be up to 1000 mm - theoretically also bigger. The system of distribution depends on the polymer output and the layer thickness: the preferred system is the helical or radial spiral distributor or, for multilayer structures, also a combination of both - if required by the application.
Coating
process vs multilayer pipes
The coating process, compared to the multilayer pipe production, enables the quick change from monolayer to multilayer, offering a high flexibility in multilayer pipes production. It makes it possible to manufacture a wide range of diameters with one head (e.g. 32-315 mm or 63-500 mm), and multiple coating and coextrusion processes are possible with more than one cross head.
With this process, thin and thick layers can be applied, adhesion can be adjusted by temperature, and the basic pipe can be manufactured with a very accurate diameter, the latter two being very important if one or more layers must be peeled off for electrofusion welding. In addition, the inner pipe has a calibrated surface.
By placing the cross heads in line, coaxial pipes can be extruded, and wires for detection can be inserted easily. The outer surface of the basic pipe can be printed, while the under pressure coating process can be performed simply, by adjusting the blower speed and without needing any vacuum generation.
Application examples
The Conextru range of cross heads includes seven types for monolayer pipes - PO 63 CR, PO 125 CR, PO 250 CR-R, PO 40 CR, PO 450 CR (top), PO 500 CR e PO 630 CR – and six types for multilayer pipes PO 2 160 CR-R, PO 2 160 CR, PO 4 160 CR, PO 3 160 CR, PO 4 180 CR e PO 3 315 CR (plus one - PO 3 630 CR - under development), where PO indicates the possibility to process polyolefins (and, in the case of multilayer types, the number next to it shows the number of layers), CR identifies the cross head technology, and R reveals the presence of a radial distributor included.
Among the application cases, the PO 4 180 CR RCS type has been used for coating a PE100 water pressure pipe with a 4 layer structure (including one barrier layer). The motor arrangement in front of it is foreseen to produce a spiral shaped colour stripe, identifying it as a barrier pipe. The PO 3 125 CR-R (centre), instead, has been utilized to produce a protection coating on a 4 layer pipe for fuel handling.
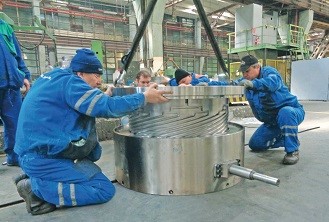