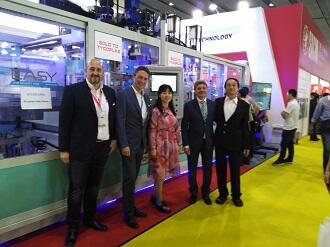
Around 10 million euros is the turnover amount achieved with the deals signed during and
immediately after the Chinaplas 2017, held in Guanghzhou in May. This is reported in a release by the Novara-based manufacturer, which also states that the deals cover the supply of thermoforming machines as well as several extruders.
“We have now a further evidence that the efforts invested in our R&D department were on the right path in developing a technology mainly devoted to flexibility in production and to high speed performances. K Show was the international platform to firstly present ACF, the last series of thermoforming machines by Amut-Comi, and the new generation of winders for stretch film cast lines. Chinaplas is the consolidation of our good reputation as manufacturer with 100% Italian technology and quality”, comments Piergianni Milani, President of the Amut Group, after the exhibition in Guangzhou and his trip to China, Cambodia and Malaysia together with Andrea Peretto, Sales Manager in charge of the Asian area.
Thermoforming
The ACF 820 thermoforming machine, exhibited in operation during Chinaplas, reaching a daily output of 260,000 lunch boxes in PP, was purchased by Tycoplas, a company leader in Malaysia for disposable articles production.
Four thermoforming machines were also purchased by SCGM, another Malaysian famous producer of disposable articles, to produce containers in PP and PET. This investment is aimed to expand the business of Lee Soon Seng Plastic Industries, SCGM’s subsidiary and another historical customer of Amut, already running nine thermoforming machines by the Novara-based manufacturer and now establishing a new building in Kulai Johor.
An Amut-Comi thermoforming machine, an AMP 630-GP model, has been chosen by SKP (Seow Khim Polyethelen), a Singapore-based player operating in the packaging industry. The machine is equipped with a 16-cavity mould for an hourly production of 22,000 cups.
Extrusion
Two twin extrusion lines from Amut to produce profiles in ABS will soon inaugurate the new Huali Industries factory, one of the biggest Chinese producers of edgebanding for furniture.
The China-based Jingmen Keshun New Material will have a complete plant for waterproofing membranes in TPO, available in 2 or 3 layers configurations and featuring a reinforcement in glass fibre or polyester. The line will reach an output of 2,200 kg/h, and will manufacture membranes with a maximum width of 2,000 mm, while the mineral filler powders will be extruded through in-line processing.
For its TPP project, the Cambodian multinational Chip Mong Group commissioned four extrusion lines for rigid, flexible and corrugated UPVC and HDPE pipes for electricity grids and sewer systems.
Finally, Klang Hock, a Malaysian converter operating in the flexible packaging industry, will install, in its new facility, a cast film line for stretch film equipped with the new ACP high-speed winder (up to 750 m/min), with a changeover cycle of just 18 seconds. The line features a width of 1.5 metres, output up to 1,100 kg/h, four extruders with L/D ratio of 1:40, a 5-layer feed unit and an automatic head.