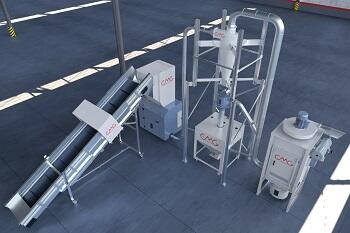
Many are the innovative and unique attributes of the new series of grinding system solutions by CMG Granulators for application with blow molding machines, and all of them contribute to obtaining the highest degree of productivity, regrind quality (homogeneous particle dimensions and absence of dust), efficiency of operation, clean environment and one of the lowest total cost of ownership (TCO). The new range is composed of 11 granulator models, all purposely designed for grinding blow molded containers or bulky objects. The standard configurations cover capacities starting from 20 kg/h all the way up to 1,500 kg/h.
11 new complete system configurations
The new series features integral infeed conveyor, metal detector, and enclosed feed chute to granulator. The infeed conveyor is integral part of the system, not anymore an appendix or an auxiliary device, and is controlled by the granulator so to synchronize all operations in full. All granulators operate in high-efficiency conditions, are all equipped with EISA premium-efficiency motors and can have AMP controls (Adaptive Motor Power). Regrind evacuation, dedusting and air filtration are all automatic and require no maintenance. Energy utilization is 20 Wh/kg against the 40 Wh/kg of conventional solutions.
Highly qualitative regrind
All CMG grinders for blow moulding applications are manufactured with the highest degree of materials and components. The unique cutting chamber is the signature feature of the new line. Totally assembled form CNC machined steel parts, fabricated with tolerances down to the hundredth of a millimeter. The high degree of precision of assembly guarantees very accurate cut, dimensional homogeneity of the regrind particles and no generation of dust. Additionally, the high precision of fabrication reduces frictions and abrasions. No cooling water is necessary, even in heavy-duty applications.
No powder generation or pollution
The regrind is evacuated from the granulator collection bin, positioned underneath the cutting chamber, by a full-vacuum regrind conveying system. Vacuum conveying through large diameter steel piping ensures no mechanical stress of the regrind with consequent absence of generation of dust. An additional key benefit is the total elimination of pollution of powdery air to the surrounding environment.
Industry 4.0 controls
The new CMG line is equipped with integral controls that monitor all functions from the moment the part to recycle is dumped on the infeed conveyor all the way the regrind is conveyed into a surge bin for subsequent utilization or into a big bag for transportation to other locations. The new controls also extend to the surge bin level management or to the automatic selection of a multiple-position filling station for big bags. All CMG Blow Moulding systems are certified for compliancy to Industry 4.0.