PA 6 a elevata fluidità per la griglia frontale della nuova Ford Kuga
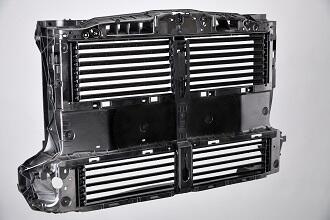
Per realizzare la griglia frontale in metallo-plastica completamente integrata della nuova Ford Kuga, il trasformatore tedesco Montaplast utilizza la PA 6 a elevata fluidità Durethan BKV30H2.0EF rinforzata con fibre di vetro di Lanxess. I termoplastici a elevata fluidità sono generalmente più costosi di quelli standard, ma risultano più vantaggiosi in termini di lavorazione, costi di produzione e libertà di progettazione.
La griglia ospita quattro saracinesche che garantiscono l’afflusso di aria al sistema di raffreddamento del motore in base alle esigenze. Il supporto contiene inserti metallici rinforzanti ai lati e nella parte superiore e ospita il fermo del cofano ad alto carico. Il compito principale dell’abbinamento metallo-plastica è quello di sostenere i sistemi di raffreddamento e tenerli in posizione, ma la griglia integra anche numerose componenti aggiuntivi quali guide, supporti per l'azionamento della regolazione e dispositivi di fissaggio.
La PA 6 offre due vantaggi principali rispetto alla possibile alternativa del PP. Anzitutto, il componente contiene diversi collegamenti filettati diretti, che sono più convenienti rispetto all'utilizzo di inserti metallici aggiuntivi; le connessioni filettate progettate con la PA 6 sono significativamente più stabili, durano più a lungo e sono più affidabili. Il secondo vantaggio è che la PA 6 resiste ai carichi termici che sorgono quando le saracinesche a griglia sono chiuse. Inoltre, grazie all'elevata fluidità della poliammide 6, le aree con geometrie in filigrana possono essere progettate con spessori più sottili, nella fattispecie ridotto fino al 20% nelle aree soggette a carichi più bassi. Rispetto a una PA 6 standard con lo stesso contenuto di fibra di vetro, questo si traduce in una notevole riduzione di peso. A causa della minore pressione di riempimento, un altro vantaggio del materiale a elevata fluidità è rappresentato dalla possibilità di produrre componenti con tensionamenti inferiori, riducendo al minimo la distorsione.