Processo ad alta temperatura per fluoropolimeri
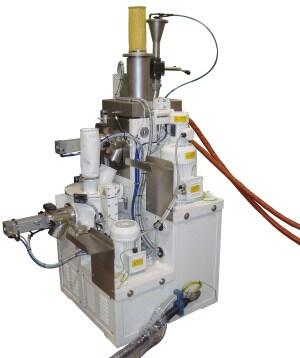
Il progetto High Temperature Bonding System (HTBS) è stato sviluppato da Plasmec per un'importante azienda del settore dei trattamenti superficiali a uso industriale, specializzata nella realizzazione di rivestimenti antiaderenti e antiusura, che richiedeva un impianto di piccole dimensioni per realizzare uno speciale ciclo di bonderizzazione (processo di adesione del pigmento - metallico - alla base, in modo da evitarne la separazione durante l'applicazione e il recupero del prodotto in cabina di applicazione) per produrre una nuova tipologia di fluoropolimero, messo a punto nei suoi laboratori di ricerca e sviluppo.
Nella prima fase dello sviluppo del progetto i tecnici si sono concentrati sulle possibili soluzioni pratiche per ottenere senza problemi un adeguato riscaldamento del materiale fino alla temperatura di processo, optando per una vasca di miscelazione dotata di un'intercapedine nella quale far fluire olio diatermico riscaldato in una centralina di termoregolazione esterna, appositamente sviluppata da un partner tecnico di Plasmec. Per il controllo della temperatura del fluido si è scelto di implementare un controllore PID e ciò ha consentito una gestione ottimale di questo importante parametro di processo. L'esigenza di lavorare a temperature elevate ha fatto sì che fosse necessario riprogettare integralmente il gruppo di trasmissione e le tenute meccaniche. Lo sviluppo di tali componenti è stato effettuato con il supporto dei più moderni strumenti di progettazione (Cad 3D, FEM e CFD), consentendo di verificarne la funzionalità già in fase di progetto. Con le stesse metodologie sono stati affrontati i problemi dell'isolamento termico della macchina e delle dilatazione termiche. Per quanto riguarda l'isolamento termico, l'obiettivo era quello di ridurre al minimo le dispersioni di calore e portare ai valori previsti dalle normative le superfici di potenziale contatto. Anche in questo caso sono stati effettuati calcoli accurati e analisi numeriche per arrivare a selezionare i corretti materiali per l'isolamento (componenti distanziali in ceramica e tessuto in fibra ceramica-silice) del miscelatore e della tubazione di collegamento con la centralina di termoregolazione. Mentre per evitare problemi legati alla dilatazione termica, grazie all'analisi delle simulazioni termiche, si sono individuate alcune zone critiche che hanno richiesto un'attenta progettazione e una corretta selezione dei materiali, facendo ampiamente ricorso alla ceramica.
Relativamente ai problemi di miscelazione e volatilità del composto, un'accurata progettazione dei singoli stadi dell'attrezzo di miscelazione, del coperchio della vasca di miscelazione, di un innovativo sistema di tenute flussate e di un elemento filtrante appositamente studiato per quest'applicazione hanno consentito di mantenere il materiale sempre confinato nel volume d'azione delle pale, anche a elevate velocità di miscelazione, con indubbi vantaggi per la dispersione e l'omogeneizzazione dei diversi componenti della miscela, come dimostrato dalle prove di laboratorio effettuate presso il cliente finale. La necessità di avere temperature di processo elevate contrastava con le esigenze legate alla sicurezza circa il pericolo d'esplosione, com'era emerso anche da una prima analisi dei rischi. Per ovviare a questo problema è stata adottata una serie di contromisure a livello progettuale che eliminasse ogni possibile fonte d'innesco, in particolare all'interno della vasca di miscelazione. Si è inoltre lavorato molto sulla selezione dei componenti idonei per questo ambiente classificato zona Atex 22 e sulla realizzazione del bordo macchina. L'analisi dei rischi condotta dopo le modifiche non ha evidenziato particolari rischi residui e, seguendo quanto prescritto dalla direttiva Atex, si è potuto dichiarare la macchina "CE EX II 2/3D IIIC T135°C".
L'esigenza di flessibilità, necessaria per poter utilizzare l'impianto per condurre prove su nuove formulazioni, è stata soddisfatta agendo a livello sia di configurazione meccanica sia di sistema di controllo. Meccanicamente si è lavorato per poter variare in maniera rapida la configurazione dell'attrezzo di miscelazione, fornendo anche diverse tipologie di pale intercambiabili. Per quanto riguarda il sistema di controllo si è cercato, mantenendo l'automazione tipica degli impianti di produzione, di renderlo il più completo possibile implementando tutta una serie di funzionalità tipiche dei laboratori, che consentiranno ai tecnici di realizzare in maniera intuitiva e rapida le ricette da processare. Per soddisfare le specifiche relative alla pulizia, il miscelatore e il raffreddatore sono stati dotati di comode bocche di scarico completamente smontabili per una rapida pulizia. Lo stesso attrezzo di miscelazione richiede un unico utensile per lo smontaggio, mentre tutta la parte meccanica e pneumatica è protetta da carter rimovibili per ridurre al minimo il deposito sui componenti di eventuali polveri presenti in atmosfera.