Afros risolve il problema degli scarti di FdC
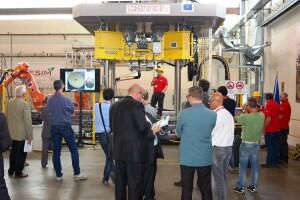
Due giornate di presentazioni dal vivo e conferenze tecniche, il 27 e 28 maggio 2014, hanno animato la sede di Afros a Caronno Pertusella con lo scopo di illustrare i primi risultati del progetto Cresim. La partecipazione è stata di oltre 80 ospiti esterni, più altrettanti dipendenti del gruppo giunti appositamente da almeno 6 diverse filiali estere e da tutte le consociate italiane. Lo staff direzionale di Afros Cannon si è detto davvero lusingato del risultato.
Il crescente uso di fibre di carbonio (FdC), dal settore automobilistico a quello aerospaziale, ha aumentato il quantitativo di scarti e rifiuti industriali. Le fonti più comuni di questi scarti sono le linee di produzione delle fibre vergini, i reparti produttivi di materiali compositi (nella fase di preformatura, in quella di impregnazione e nella fase di rifilatura) e le aree di stoccaggio di pezzi giunti al termine del loro impiego utile. Centinaia di tonnellate di questi prodotti vengono conferite ogni anno in discariche autorizzate, sprecando così il loro rilevante costo originario e aggiungendo il costo per lo smaltimento. In genere tali sprechi vengono conteggiati nel costo industriale e ribaltati sul consumatore finale oppure, nel caso di veicoli militari, sul contribuente.
Le FdC riciclate sono invece oggi commercialmente disponibili presso diversi fornitori specializzati, sia in Italia che in Germania, Inghilterra e Francia. Il costo del prodotto riciclato si avvicina al 50% del costo delle FdC vergini, riducendosi ulteriormente per quantitativi medio-grandi: questo fattore, da solo, lo rende estremamente interessante per i produttori di articoli in materiali compositi.
Il problema è ottenere da queste FdC un prodotto a elevate caratteristiche fisico-meccaniche ed estetiche, per non essere costretti a utilizzarle per applicazioni secondarie, a basso valore aggiunto. E questo è esattamente l'oggetto di un progetto di ricerca e sviluppo finanziato dall'UE nell'ambito del Programma LIFE+, uno strumento finanziario della Comunità Europea che supporta il miglioramento e la difesa dell'ambiente attraverso progetti gestiti da imprese private e/o enti locali, che li gestiscono sotto il controllo scrupoloso di esperti della CE. In tale ambito, nel 2012 ha intrapreso il progetto CRESIM (Carbon Recycling by Epoxy Special Impregnation), il cui obiettivo finale è lo sviluppo di un processo per la produzione di CFRP (Carbon Fibres Reinfroced Plastics) di elevata qualità partendo da FdC riciclate.
Per questo il management di Cannon ha definito un importante investimento in aree di laboratorio, nuove attrezzature e giorni/uomo di personale specializzato, coinvolgendo due aziende del gruppo: Afros e Cannon Ergos. Si è iniziato mettendo a disposizione di queste tecnologie una ampia parte del rinnovato Centro R&D per i compositi di Caronno Pertusella, a nord di Milano, dove è stata installata la pressa con piani riscaldabili ad alta temperatura ed elevata forza di chiusura, che permette oggi l'utilizzo di stampi di campionatura di ampie dimensioni, così come il montaggio di stampi di produzione forniti dai potenziali clienti interessati a sviluppare insieme nuove applicazioni.
In quest'area sono stati installati due robot antropomorfi a 6 assi di ABB, per la manipolazione dei rinforzi in FdC riciclata e la movimentazione delle teste di miscelazione, necessarie per le operazioni d'iniezione in stampo chiuso o di deposizione in stampo aperto della formulazione reattiva.
I prodotti chimici necessari per le diverse prove di impregnazione ad alta reattività (formulazioni a base di poliuretano o di resine epossidiche) vengono dosati con assoluta precisione da due diverse unità dosatrici Cannon ad alta pressione e bassa portata istantanea, capaci di operare in modalità completamente autoregolata e controllo elettronico in closed-loop. Lo staff di specialisti che ha sviluppato nel recente passato una linea completa di attrezzature per lo stampaggio rapido con tecnologia RTM (Resin Transfer Moulding) è stato assegnato a questo progetto, con un elevato grado di priorità. L'impianto pilota appena descritto è in grado di produrre prototipi e parti in CFRP da FdC riciclate - industrialmente utilizzabili - molto più ampi delle campionature di prova realizzate fino a qualche mese fa nello stesso laboratorio.
I primi risultati industriali
I primi risultati pratici del progetto Cresim si sono materializzati nella definizione di un progetto congiunto di sviluppo con la società Loson di Rescaldina (VA), che opera nel campo dei materiali compositi, fornendo parti stampate in CFRP per utilizzi civili e per la difesa. Utilizzando FdC riciclate fornite dalla società Ferrari Carbon di Milano e uno stampo realizzato appositamente da un fornitore specializzato, la DMC di Carate Brianza, è stato messo a punto il progetto per una parabola componibile sul campo per trasmissioni satellitari, utilizzabile per impieghi civili o militari. Costituita da sette spicchi uguali, la parabola, del diametro di 130 cm, può essere trasportata comodamente in un grosso zaino e assemblata in pochi minuti una volta giunti sul luogo delle operazioni.
Il disegno arrotondato degli spicchi è stato scelto per ottimizzare la ricezione dei segnali digitali e minimizzare i potenziali problemi derivanti da forti venti o da vibrazioni derivanti dagli automezzi su cui potrebbe essere installata. La produzione di uno spicchio di questa parabola è stata mostrata dal vivo il 27 e 28 maggio proprio sulla linea messa a punto da Afros nella propria sede.
I vantaggi della tecnologia Cresim
I principali vantaggi derivanti dall'utilizzo della tecnologia Cresim si possono riassumere in:
- risparmi in materia prima: la FdC riciclata è oggi disponibile a circa metà del costo di quella vergine, da diverse fonti europee
- risparmi nei costi di smaltimento: mandare in discarica le FdC significa buttar via una materia prima costosa e pagare anche per l'operazione; conferire i propri scarti a un riciclatore permette di convertire un costo in un ricavo
- riduzione dell'impatto energetico e ambientale della propria produzione: l'elevata quantità d'energia consumata durante la produzione della FdC originale può essere riutilizzata durante la sua "seconda vita", evitando così che una uguale quantità d'energia venga sprecata a ogni ciclo di vita di un prodotto simile realizzato con FdC
- ottimizzazione della struttura combinando, in un "materassino" di rinforzo, uno strato esterno sottile di FdC vergine e uno interno più spesso di FdC riciclata, per ottenere contemporaneamente parti strutturali robuste ed esteticamente piacevoli
- riduzione del tempo di ritorno sull'investimento in presse e unità dosatrici: la possibilità di accelerare i tempi d'estrazione (dai tradizionali 30 min del processo RTM ai 3 min ottenibili con processo Cannon Estrim) consente di ammortizzare le attrezzature produttive molto più velocemente
- risparmi energetici nelle fasi di preformatura dei rinforzi, di impregnazione e di polimerizzazione: i preformatori utilizzati per dar forma ai rinforzi in FdC sono macchine semplici e poco impegnative dal punto di vista energetico; il processo d'impregnazione non richiede una messa a punto complessa o l'utilizzo di vuoto
- quando si usano le tecniche a stampo aperto Estrim LLD e SLD si hanno ulteriori vantaggi: la tecnologia utilizza basse pressioni durante la chiusura dello stampo in pressa, per cui si possono utilizzare motori meno potenti; Le unità dosatrici operanti a temperatura vicina a quella ambiente non richiedono elevate potenze elettriche installate per scaldare i materiali; Si possono usare stampi in resina o in alluminio, molto meno costosi dei classici stampi in acciaio.