Dieci estrusori alimentati da un unico impianto
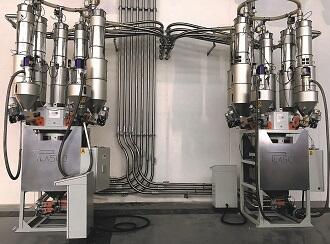
Il costruttore ferrarese di dosatori volumetrici e gravimetrici, sistemi di trasporto e impianti centralizzati, Plasco, ha messo a punto un impianto di dosaggio centralizzato per un'importante produttore di film tecnico destinato all’imballaggio alimentare e non, con una capacità produttiva di 2000 kg all’ora. Il sistema è stato studiato per alimentare 10 linee di estrusione impostando una ricetta diversa per ogni linea, scegliendo fra otto materiali vergini.
Nello specifico, Plasco ha progettato e realizzato due stazioni gravimetriche su misura per la preparazione delle premescole e la gestione di tutti i passaggi dei materiali dai silos all'estrusore. I materiali vengono prelevati dai silos con un impianto di alimentazione centralizzato e stoccati all'interno delle tramogge della stazione gravimetrica. Quando l'impianto riceve la richiesta di materiale dall'estrusore, i dosatori a coclea inviano il "batch" all'interno di una bilancia. Una volta ultimata, la ricetta viene scaricata in una vasca di convogliamento e immediatamente trasportata all'interno del mescolatore posizionato sopra all'estrusore che aveva fatto la richiesta. In seguito, all'interno della bilancia e della vasca viene effettuata una pulizia per mezzo di un sistema ad aria compressa, per evitare la contaminazione tra materiali diversi.
Il sistema completamente automatico azzera gli scarti di produzione dovuti alla preparazione manuale delle ricette. Tutto il processo viene gestito da un PLC Siemens di ultima generazione con un software progettato internamente. L'interfaccia utente, resa intuitiva da una grafica tridimensionale che rispecchia l’impianto, è realizzata con un panel-PC touch screen di 12 pollici. L’operatore deve impostare solo le percentuali di ogni materiale e associare la ricetta alla linea di destinazione: il sistema risulta completamente autonomo grazie a un algoritmo che rende sicuri la preparazione e il trasferimento delle ricette di lavorazione.
In questo caso specifico è stato realizzato un protocollo di
comunicazione per lo scambio dei dati con il gestionale dell’azienda, secondo i
requisiti di Industria 4.0. Inoltre, è possibile tracciare i vari materiali
utilizzati nelle diverse ricette. Il quadro elettrico è equipaggiato di un
modulo per l'assistenza da remoto, così da dare, in caso di necessità, supporto
immediato al trasformatore.
Il sistema di Plasco ha permesso di ottenere diversi vantaggi economici e produttivi: uno stabilimento pulito ed efficiente; una migliore qualità del prodotto finito; la possibilità di utilizzare le risorse interne in modo più razionale. Soprattutto, il trasformatore ha potuto abbattere i costi dovuti all’elevata quantità di materiale di scarto che si generava durante la preparazione delle miscele prima di avviare il nuovo impianto.
Recentemente Plasco ha acquisito un’azienda specializzata in automazione industriale basata sullo sviluppo software PLC-PC, di controlli di processo, di quadri elettrici per impianti e macchine automatiche. Questa operazione ha permesso al costruttore di allargare la propria gamma di soluzioni, offrendo un servizio hardware e software a 360°.
“Oggi la nostra azienda è in grado di offrire flessibilità e competenza che ci permettono di assistere il cliente in modo professionale, proponendo il miglioramento tecnico e qualitativo dei processi di produzione. La realizzazione di questo complesso impianto di dosaggio e trasporto ne è la conferma” ha affermato Martina Giatti, direttore commerciale di Plasco.