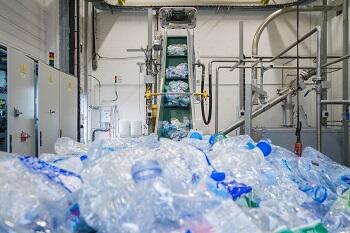
Sidel has opened a new hub dedicated to PET recycling. At its unique small-scale PET recycling pilot line in Octeville (France), the company will develop its understanding of PET recycling with the aim of giving comprehensive support to the market as it switches to greater use of recycled PET.
Seeking carbon neutrality, the packaging industry is in the middle of a transition period that aims to replace virgin PET with recycled PET. Sidel is engaging with this transition to circular packaging solutions, enabling rPET to be more widely used. The unique small-scale PET recycling line will allow the company to develop advanced knowledge about the recycling of food-contact PET bottles. As Sidel packaging experts assess the impact of additives and primary packaging materials on rPET resin the facility will become an important reference for raw material producers, recyclers and recycling regulatory organisations. The line will also enable Sidel to further develop its own knowledge, ideas and innovative packaging solutions.
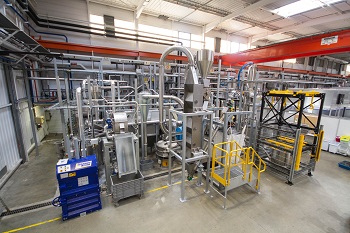
Demand for rPET is increasing and the market is developing as brand owners seek carbon neutral solutions. The amount of recycled PET in packaging globally has increased to 8% compared to 5% in 2018. In Europe, the average is already 15% and is projected to grow to 35% in 2030.
“There is a big move towards recycled PET, but demand is outstripping supply,” said Naima Boutroy, Sidel Global Packaging Expert. “The market still has a lot to learn and we can provide valuable insights. There is a variability in recycled PET resin grades, and standardisation is still in development. We need to address this to create the best possible finished bottles. Our line will test the recyclability of post-consumer PET bottles from different feed stocks, including additives and caps as well as labels, inks and glue. We will be working with traditional Sidel customers such as brand owners, converters and co-packers, as well as other suppliers like raw material producers, recyclers and regulatory organisations, to enable the scaling-up of rPET capacity. We can also check any innovations comply with bottle-to-bottle recycling.”
Sidel new line will take raw material from industrial partners such as sorting facilities, recyclers and brand owners. It will then recreate and study all aspects of the process from bales to flakes including pellets ready to be injected into preform, injection and blow moulding.
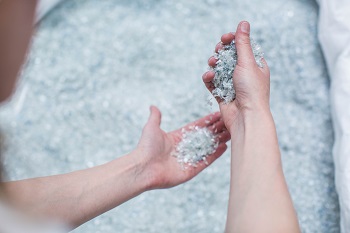
The company will give the packaging industry the opportunity to access a fully equipped pilot line. This line covers every step of the recycling process: from washing, drying and pellet extrusion, to solid-state polymerisation, including dedicated process and laboratory controls at every step.
PET is proven to be recyclable and is the only food-safe bottle-to-bottle recycled material, but the market has yet to see the production of standardised rPET resin grade in high quantities; achieving this could facilitate the market conversion from virgin PET to rPET. Lifecycle analysis shows that PET already has the best carbon footprint among materials currently available; creating a robust recycling loop to achieve full circularity at scale will make PET an even more sustainable choice.
The line, which has a holistic bottle-to-bottle approach, is just one of a range of services that Sidel is establishing under the name RePETable services. The services will draw upon Sidel 40 years of blowing and packaging expertise, to support brand owners and convertors in producing rPET bottles through line upgrade solutions, packaging optimisation, blowing process qualification, troubleshooting, rPET processing training.