I braccioli centrali per interni auto diventano ultraleggeri con Flexflow
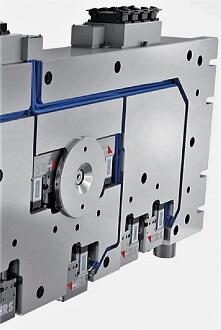
La produzione del bracciolo ultraleggero per interni auto è uno degli ultimi esempi applicativi della tecnologia Flexflow sviluppata dal fornitore di canali caldi HRSflow, parte di Gruppo INglass. Il processo multifase combina la termoformatura di una foglia in materiale composito con lo stampaggio a iniezione di due differenti materiali termoplastici. I partner che hanno contribuito allo sviluppo di questo progetto sono il costruttore tedesco di presse KraussMaffei e lo stampista statunitense Proper Tooling.
La struttura portante del bracciolo centrale è ottenuta grazie al processo FiberForm sviluppato da KraussMaffei, in cui una sottile foglia in materiale rinforzato con fibre viene riscaldata, inserita nello stampo e termoformato. I due successivi processi di iniezione sono realizzati grazie alla tecnologia a tavola rotante che consente l’iniezione contemporanea nei due lati opposti dello stesso stampo. In una prima fase, il supporto è sovrastampato con polipropilene. Se ne ottiene un componente stampato con una geometria quasi definitiva, compresi gli elementi di fissaggio. La struttura in PP è successivamente sovrastampata con un elastomero termoplastico nella sezione opposta dello stampo. Questo consente di ottenere un bracciolo centrale con una finitura superficie di elevata qualità ottica e tattile.
In entrambe le fasi del processo di iniezione è utilizzata la tecnologia Flexflow con due iniettori nella prima fase e tre nella seconda. La possibilità di controllare in modo indipendente ciascun otturatore consente un riempimento ottimale delle cavità dello stampo, garantendo un’alta affidabilità di processo e la fattibilità a livello economico.
Il sistema a otturazione comandata elettricamente Flexflow
permette di regolare con precisione i parametri di processo. Per esempio, è
possibile controllare ciascun otturatore di un sistema a canale caldo in modo
indipendente dagli altri aggiustandone con precisione la posizione, la velocità
e la forza. Questa soluzione garantisce un controllo accurato, flessibile e
facile della pressione e del flusso del materiale durante l’intero processo di
stampaggio, ottimizzando la qualità del prodotto finito. Tra i vantaggi che ne
derivano rispetto al tradizionale sistema a canale caldo pneumatico o
idraulico, rientrano la possibilità di ottenere superfici di Classe A senza
imperfezioni o deformazioni. Un altro beneficio è rappresentato dalla riduzione
della manutenzione e dalla facilità di utilizzo. Il tonnellaggio della pressa
può essere ridotto indicativamente del 20% e il peso del componente stampato
fino al 5%, assicurando comunque l’elevata ripetibilità del processo, fattore
fondamentale per la produzione in larga scala.